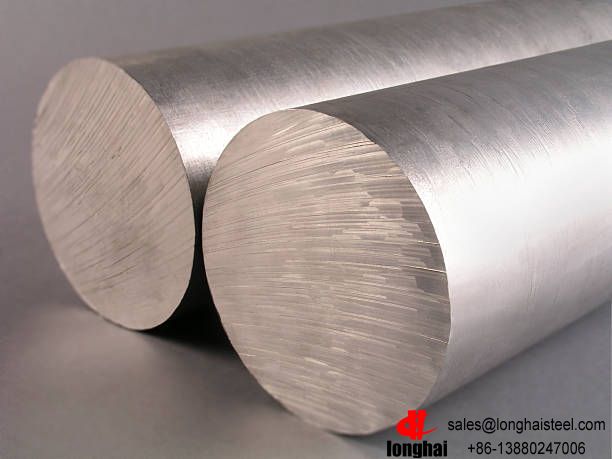
Inconel 718 is a high-strength, corrosion-resistant nickel-chromium alloy. It is commonly used in high-temperature applications such as gas turbines, jet engines, and nuclear reactors, as well as in the aerospace, defense, and oil and gas industries. AMS 5596, AMS 5597
What is Inconel 718 grade steel?
Inconel 718 is a high-strength, corrosion-resistant nickel-chromium alloy. It is commonly used in high-temperature applications such as gas turbines, jet engines, and nuclear reactors, as well as in the aerospace, defense, and oil and gas industries. Inconel 718 is known for its excellent mechanical properties at high temperatures, which include high tensile strength, fatigue resistance, and creep resistance. It can withstand temperatures up to 1300°F (704°C) and is highly resistant to oxidation and corrosion in harsh environments. The alloy is made up of nickel, chromium, iron, molybdenum, niobium, and small amounts of aluminum and titanium. It is typically produced by a process called vacuum induction melting followed by vacuum arc remelting, which produces a highly uniform and fine-grained material. Inconel 718 has a range of applications, including in aircraft engines, gas turbine components, rocket motors, and pressure vessels. It is also used in oil and gas extraction equipment and nuclear reactors.
AMS 5589, ASTM B637, GE B50TF15 AMS 5590, ASTM B670, PWA 1009 AMS 5596, DIN 2.4668 PWA 1010 AMS 5597, DIN 2.4688 PWA 1033 AMS 5662, GE B14H89, RBO 170-153 AMS 5663, GE B50 TF14 SPS M275 AMS 5664, GE B50 TF69 SPS M637 AMS 5832, GE B50TF14, use Gas turbines, Turbo pump seals, Spacecraft, Rocket motors, Nuclear reactors, Tooling.
Products Form:
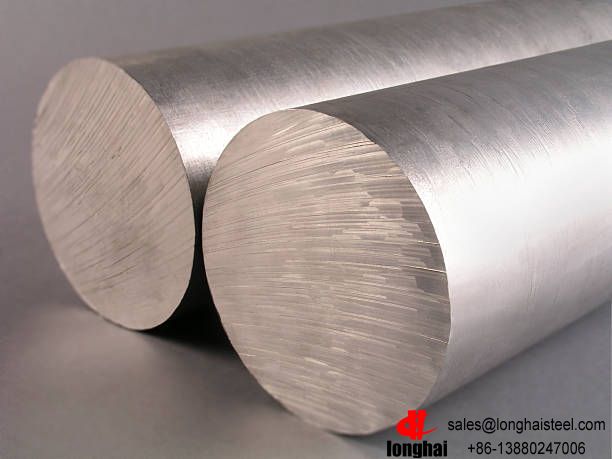
Chemical Composition
Grade | Chemical composition WT % | |||||||||||||
---|---|---|---|---|---|---|---|---|---|---|---|---|---|---|
C | Si | Mn | P | S | Cr | Ni | Mo | Nb | Ti | Al | Co | B | Cu | |
Inconel 718 | 0.02-0.08 | 0.35 | 0.35 | 0.015 | 0.015 | 17-21 | 50-55 | 2.8-3.3 | 4.75-5.50 | 0.65-1.15 | 0.2-0.8 | 1.00 | 0.006 | 0.30 |
Mechanical Properties
Inconel 718 Mechanical properties
- Hardness: 310-390 HV 10 (Solution heat treated + Cold rolled)
- Hardness after precipitation Hardening: 450-530 HV10
Precipitation Hardening cycle: 720°C± 10°C for 8 hrs, 2hrs controlled cooling with appx. 50°C/HRS,620°C±10°C for 8 hrs, air cooled
Properties | Metric | Imperial |
---|---|---|
Tensile strength (Precipitation hardened) | 1375 MPa | 199400 psi |
Yield strength (Precipitation hardened) | 1100 MPa | 160000 psi |
Elongation at break (Precipitation hardened) | 25% | 25% |
Physical Properties
Density | ||
Specific Gravity | ||
Melting Range |
Heat Treatment
Solution Treatment: 1800°F (982°C) 1 hour
Precipitation Treatment: 1325°F (718°C) 8 hours, Furnace Cool at 100°F (55°C) per hour to 1150°F (621°C) 8 hours
Thermal Properties
Welding Properties
Inconel 718 alloy can be welded using gas-tungsten arc welding, shielded metal arc welding, submerged-arc welding and gas metal-arc welding methods.
Machining Properties
Inconel 718 alloy can be machined using conventional machining techniques used for iron based alloys.
What is Inconel 718 equivalent to?
AMS 5589, ASTM B637, GE B50TF15 AMS 5590, ASTM B670, PWA 1009 AMS 5596, DIN 2.4668 PWA 1010 AMS 5597, DIN 2.4688 PWA 1033 AMS 5662, GE B14H89, RBO 170-153 AMS 5663, GE B50 TF14 SPS M275 AMS 5664, GE B50 TF69 SPS M637 AMS 5832, GE B50TF14