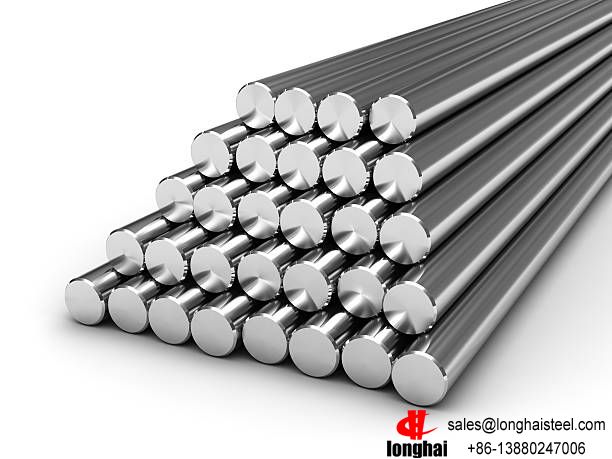
40CrMoV4-6, 1.7711 is a low-alloy steel grade commonly used in the construction of pressure vessels and boilers According to the EN 10269
What is 40CrMoV4-6, 1.7711 grade steel?
According to the EN 10269, 40CrMoV4-6, 1.7711 is an alloy steel for thermal and mechanical processing. It has high strength, heat resistance and wear resistance. This kind of steel can be used to manufacture parts that work under high temperatures and pressures, such as automotive engine parts, cylinders, bearings, gears, etc. the steel needs to be heat treated to obtain the required mechanical properties.
Impact toughness: The impact toughness of this grade can be around 27 Joules at room temperature.
Hardness: The hardness of 40CrMoV4-6 steel is typically in the range of 160 to 190 HB.
Some common applications of 40CrMoV4-6 include:
Automotive industry: It is used in the production of various automotive components such as gears, shafts, axles, and connecting rods due to its high strength and fatigue resistance.
Aerospace industry: It is used in the manufacturing of aircraft landing gear components, engine parts, and structural components that require high strength and toughness.
Oil and gas industry: 40CrMoV4-6 is used in the production of drill collars, drill bits, and other equipment used in oil and gas drilling operations due to its high strength and resistance to wear and corrosion.
Power generation industry: It is used in turbine components and power transmission equipment that require high strength and resistance to thermal and mechanical stresses.
Tool and die industry: 40CrMoV4-6 is often used in the production of molds, dies, and cutting tools that require high hardness, wear resistance, and toughness.
Overall, 40CrMoV4-6 is a versatile steel that finds applications in various industries where high strength, toughness, and resistance to wear and fatigue are required.
Products Form:
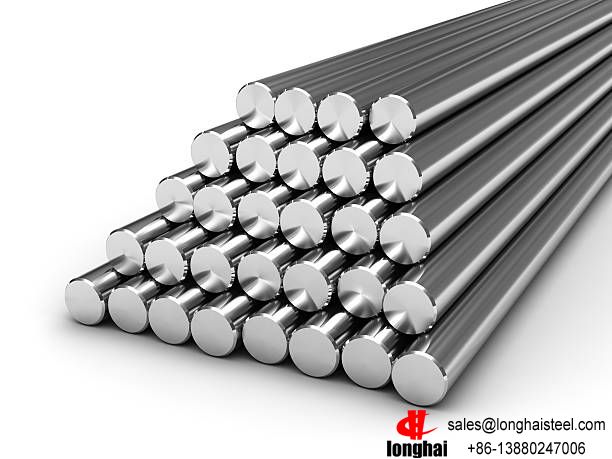
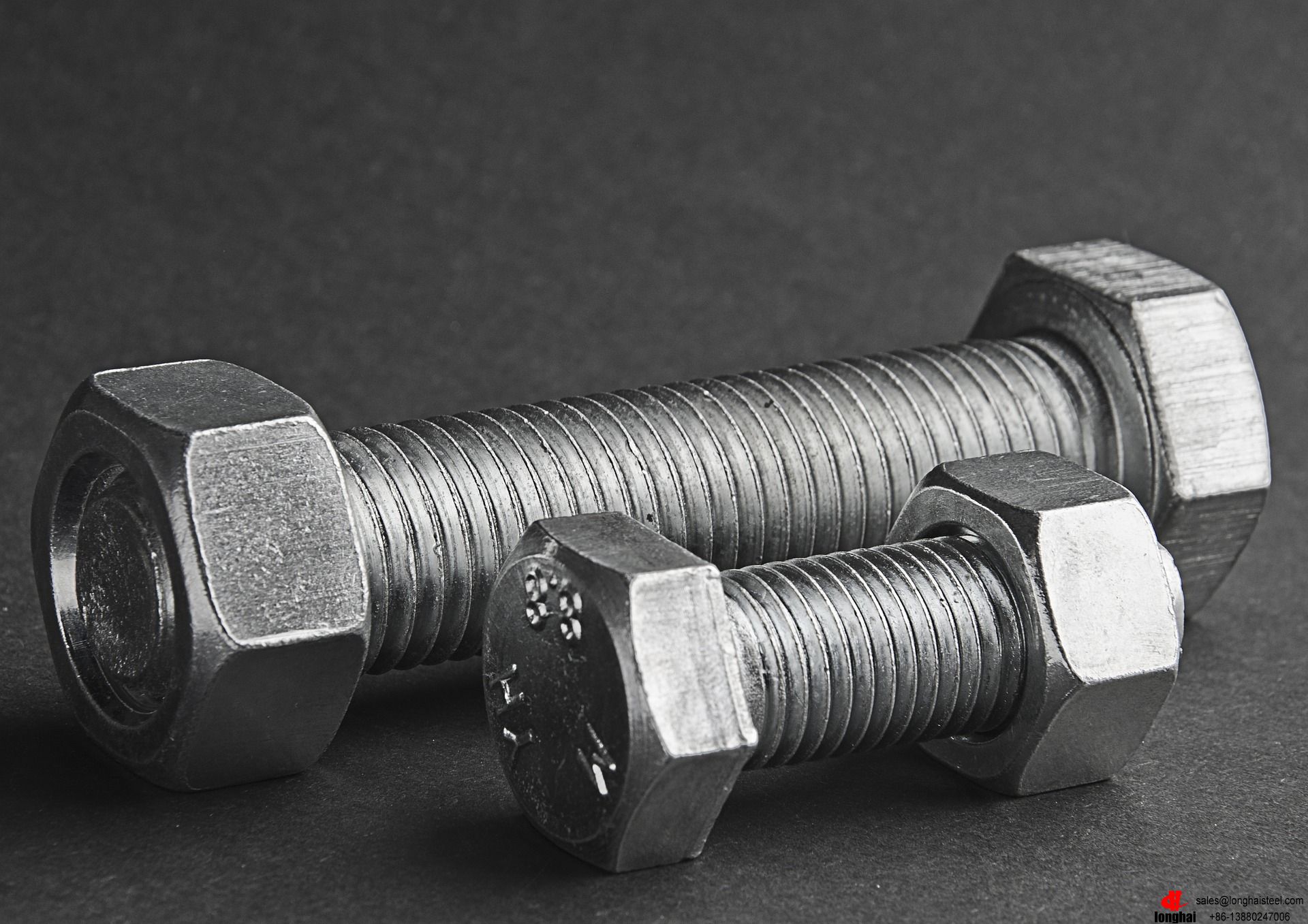
Chemical Composition
Grade | Chemical composition WT % | ||||||||
---|---|---|---|---|---|---|---|---|---|
C | Mn | Si | P | S | Cr | Mo | V | Al | |
40CrMoV4-6, 1.7711 | 0.36 - 0.44 | 0.45 - 0.55 | max. 0.4 | max. 0.025 | max. 0.030 | 0.9 - 1.2 | 0.50 - 0.65 | 0.25 - 0.35 | max. 0.015 |
SA193 / A193 gr. B16, SA194 / A194 gr. 16 | 0.36 - 0.47 | 0.45 - 0.70 | 0.15 - 0.35 | max. 0.035 | max. 0.040 | 0.80 - 1.15 | 0.50 - 0.65 | 0.25 - 0.35 | max. 0.015 |
UNS K14072 | 0.36 - 0.44 | 0.45 - 0.70 | 0.15 - 0.35 | max. 0.040 | max. 0.040 | 0.80 - 1.15 | 0.50 - 0.65 | 0.25 - 0.35 | max. 0.015 |
Mechanical Properties
The mechanical properties of 40CrMoV4-6 are as follows:
- Tensile strength: 900-1100 MPa
- Yield strength: 750-900 MPa
- Elongation: 14-18%
- Reduction of area: 45-55%
- Hardness: 300-350 HB
- Impact toughness: 27-35 J/cm2
- Fatigue strength: 500-600 MPa
It is important to note that these values may vary depending on the specific heat treatment and processing conditions.
Physical Properties
The physical properties of 40CrMoV4-6 are as follows:
- Density: 7.85 g/cm3
- Melting point: 1420-1460°C
- Thermal conductivity: 41.9 W/m·K
- Specific heat capacity: 460 J/kg·K
- Electrical conductivity: 27.5% IACS (International Annealed Copper Standard)
- Magnetic properties: It is not a magnetic material in its annealed or tempered state.
Please note that these values are approximate and can vary depending on the specific manufacturing process and conditions.
Heat Treatment
40CrMoV4-6 can be heat treated using the quench and temper (QT) process to improve its mechanical properties. The specific heat treatment parameters may vary depending on the desired properties and the material's initial condition. Here is a general guideline for the QT process:
Preheating: The material is preheated to a temperature between 650°C and 700°C for a sufficient amount of time to ensure uniform temperature throughout the part.
Quenching: The preheated material is rapidly cooled by immersion in a quenching medium such as oil, water, or polymer. The quenching medium should be chosen based on the desired hardness and distortion control.
Tempering: After quenching, the material is tempered to relieve internal stresses and improve its toughness and ductility. The tempering temperature should be selected based on the desired balance between hardness and toughness.
Cooling: The part is then air-cooled to room temperature.
The specific temperatures and holding times during the heat treatment process can vary depending on the steel grade and the desired mechanical properties. It is recommended to consult the material's technical data sheet or work with a heat treatment specialist to determine the optimal heat treatment parameters for 40CrMoV4-6 in the QT process.
Thermal Properties
Welding Properties
40CrMoV4-6 steel can be welded using various welding processes such as arc welding, gas welding, and resistance welding. However, it is important to consider the following factors when welding this steel: Preheating: Preheating the material before welding can help reduce the risk of cracking and improve the weldability. The preheating temperature should be around 200-300°C, but it may vary based on the thickness and composition of the material. Welding process: The recommended welding processes for 40CrMoV4-6 are shielded metal arc welding (SMAW), gas tungsten arc welding (GTAW/TIG), and gas metal arc welding (GMAW/MIG). These processes provide good control over heat input and allow for the use of suitable filler materials. Filler material: The filler material used for welding 40CrMoV4-6 should have similar or equivalent mechanical properties to the base metal. Commonly used filler materials include ER80S-B2 and ER90S-B3. It is crucial to select the appropriate filler material to ensure good weld integrity and mechanical properties. Post-weld heat treatment: After welding, it is recommended to perform post-weld heat treatment to relieve residual stresses and improve the material's mechanical properties. The specific heat treatment parameters may depend on the desired properties and the welding procedure used. Weld quality and inspection: It is important to ensure proper weld quality by following standard welding procedures, maintaining proper weld joint preparation, and conducting non-destructive testing (such as visual inspection, ultrasonic testing, or radiographic testing) to detect any defects or discontinuities. It is essential to consult the material's technical data sheet and follow the recommended welding procedures provided by the steel manufacturer or welding experts to ensure successful and reliable welds. Additionally, it is advisable to work with experienced welders and adhere to relevant welding codes and standards.
Machining Properties
When machining 40CrMoV4-6 steel, it is important to consider its high hardness and toughness. Here are some guidelines for machining this material:Tool selection: Choose cutting tools that can withstand high cutting forces and provide good chip control. Carbide inserts with high-speed steel substrates or coated carbide inserts are commonly used. Consider using tools with a positive rake angle to reduce cutting forces.Cutting parameters: Optimize the cutting parameters based on the specific machining operation, such as turning, milling, or drilling. Adjust the cutting speed, feed rate, and depth of cut to achieve the desired surface finish and tool life. Slow cutting speeds are generally recommended due to the high hardness of the material.Cooling and lubrication: Use a suitable cutting fluid or coolant during machining to reduce heat buildup and extend tool life. Cooling and lubrication help prevent tool wear, improve chip evacuation, and reduce the risk of workpiece distortion.Workpiece stability: Ensure the workpiece is properly secured and stable during machining operations to minimize vibrations and maximize accuracy. Use sturdy fixtures and clamping methods to prevent workpiece movement or chatter.Post-machining treatment: Due to the high hardness of 40CrMoV4-6 steel, post-machining treatments like stress relieving or tempering may be necessary to reduce residual stresses and enhance the material's mechanical properties. Consult the material's technical data sheet or seek expert advice for the appropriate post-machining treatment.Quality control: Regularly inspect the machined components for dimensional accuracy, surface finish, and any defects. Use appropriate measuring instruments to ensure the machined parts meet the required specifications.It is advisable to consult with machining experts or follow the recommendations provided by the steel manufacturer for specific machining requirements and techniques. Additionally, working with experienced machinists and adhering to relevant machining codes and standards is crucial for achieving optimal results.
What is 40CrMoV4-6, 1.7711 equivalent to?
The steel grade 1.7711 is commonly known as 40CrMoV4-6. It is a low alloy steel that is primarily used for applications requiring high strength and toughness, such as in the manufacturing of heavy-duty machinery components and tools.Here are some similar grades to 1.7711:42CrMo4 (1.7225): This is a widely used chromium-molybdenum alloy steel that has similar properties to 1.7711. It offers high strength, good toughness, and excellent wear resistance. 42CrMo4 is often used in applications where high tensile strength and fatigue resistance are required, such as in the automotive and aerospace industries.4140 (UNS G41400): This is another popular chromium-molybdenum alloy steel that shares similar characteristics to 1.7711. It is known for its excellent hardenability, high tensile strength, and good impact resistance. 4140 is commonly used in applications such as gears, shafts, and other structural components.34CrMo4 (1.7220): This is a low-alloy steel grade that contains chromium and molybdenum, similar to 1.7711. It offers good strength, toughness, and wear resistance. 34CrMo4 is often used in the manufacturing of pressure vessels, pipes, and other components in the oil and gas industry.35CrMoV5-7 (1.7709): This steel grade is also similar to 1.7711 in terms of its alloy composition and mechanical properties. It is commonly used for applications requiring high strength, good toughness, and resistance to fatigue and wear.When selecting a similar grade to 1.7711, it is important to consider the specific requirements of your application, including the desired mechanical properties, heat treatment capabilities, and availability of the material. It is always recommended to consult with steel suppliers or materials engineers to determine the most suitable grade for your specific needs.