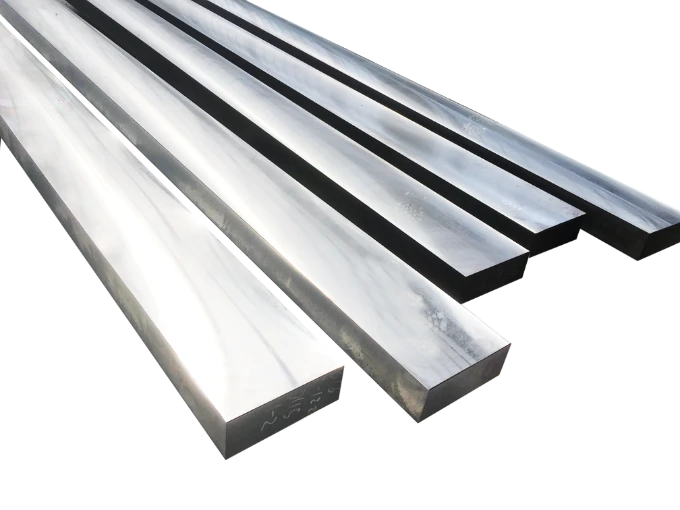
AISI 422, SUH 616, B4B, 1.4935, X20CrMoWV12-1 Turbine Blades acc.to B50A951 A1, A2, SIEMENS 10705BL/M, 10705BR, 10705BU. ASME SA-437 Alloy Steel Turbine-Type Bolting Material Specially Heat Treated for High-Temperature Service, ASTM A437, ASTM A565, JIS G4311, SAE J 775
What is AISI 422, S42200, 616 grade steel?
AISI 422, Alloy 616, 1.4935, X20CrMoWV12-1 creep resistant martensitic stainless steels are high-alloy steels that exhibit better corrosion resistance than other steels, 12% Chromi um stainless steel used for thermal engine components in power plants, mainly turbine blades, Steam Turbine buckets, bolting fasteners, valves, and other miscellaneous components. Max temperature for continous operating is 580 °C.Chrome-nickel steel with an austenitic structure with carbides. Alloying additions of molybdenum, vanadium and tungsten increase the melting temperature, thus having a positive effect on creep resistance. acc.to B50A951 A1, A2, SIEMENS 10705BL/M, 10705BR, 10705BU. ASME SA-437 Grade B4B Alloy Steel Turbine-Type Bolting Material Specially Heat Treated for High-Temperature Service. ASTM A437 Grade B4B Stainless and Alloy-Steel Turbine-Type Bolting Specially Heat Treated for High-Temperature Service. ASTM A565 Grade 616 Martensitic Stainless Steel Bars for High-Temperature Service. JIS G4311 SUH 616 Heat-resisting steel bars and wire rods. SAE J 775 SUH 616 Engine poppet valve information report.
Melt Practice: EAF+AOD+IC+ESR
Understanding the Versatility and Applications of AISI 422, 616, and Other Stainless Steels
Stainless steel is an essential material used across various industries due to its durability, resistance to corrosion, and versatile applications. Among the many grades available, AISI 422, AISI 616, SUH 616, B50A951, 1.4935, and X20CrMoWV12-1 stand out. This article explores these grades in detail, discussing their unique characteristics and uses.
What is AISI 422 Stainless Steel?
AISI 422 is a high-chromium, martensitic stainless steel that offers excellent resistance to oxidation and corrosion. It is commonly used in applications that require good wear resistance and high strength. Due to its high chromium content, AISI 422 performs well in environments with moderate corrosive conditions. This grade is often used in the manufacturing of turbine blades, shafts, and other critical components where strength and corrosion resistance are essential.
AISI 616: High-Performance Stainless Steel
AISI 616 is another important stainless steel grade, offering a unique combination of properties. Known for its excellent strength and corrosion resistance, AISI 616 is used in industries such as aerospace and power generation. Its ability to withstand high temperatures and corrosive environments makes it ideal for turbine components and other high-stress applications. AISI 616 also provides good toughness, making it a reliable choice for demanding environments.
SUH 616: Japanese Stainless Steel Grade
SUH 616 is a Japanese stainless steel grade that is closely related to AISI 616. This grade offers similar properties but is often chosen for its specific applications in high-temperature environments. Like AISI 616, SUH 616 excels in resisting corrosion and maintaining its mechanical properties under stress. It is commonly used in the manufacturing of gas turbines and high-temperature components in the power generation sector.
B50A951: Aerospace and Turbine Steel
B50A951 is a specialized stainless steel grade that plays a crucial role in the aerospace and turbine industries. This steel is designed to withstand extreme temperatures and pressure conditions. It offers high strength, oxidation resistance, and durability, making it perfect for critical aerospace components. Engineers often choose B50A951 for turbine blades, exhaust components, and other high-performance parts where reliability is paramount.
1.4935: European Steel for High-Temperature Applications
1.4935 is a European steel grade known for its exceptional performance in high-temperature applications. It is widely used in industries like power generation, where components must endure extreme heat and corrosive environments. The steel’s high resistance to oxidation and ability to maintain its structural integrity under stress makes it an essential material in the manufacturing of turbine blades, rotors, and other high-temperature parts.
X20CrMoWV12-1: High-Temperature and Pressure Resistant Steel
X20CrMoWV12-1 is a steel grade often used in applications requiring both high temperature and pressure resistance. With its excellent toughness and ability to withstand thermal stress, this material is ideal for power plants and other high-performance systems. This steel grade is highly resistant to corrosion, making it a reliable choice for parts exposed to extreme conditions in gas turbines and other heavy machinery.
Key Properties and Benefits of Stainless Steel Grades
Each of these stainless steel grades offers a unique combination of strength, corrosion resistance, and temperature tolerance. Whether you’re designing components for aerospace, power generation, or other critical industries, these materials provide the reliability needed for high-stress applications. Stainless steel’s ability to resist rust, corrosion, and wear ensures that components remain durable and functional even in the harshest environments.
Applications Across Industries
These stainless steel grades find their place in a wide variety of industries. AISI 422 and AISI 616 are often used in power generation for turbine blades and shafts, where high strength and corrosion resistance are critical. SUH 616 and B50A951 are popular in the aerospace sector, where reliability and performance are non-negotiable. Similarly, 1.4935 and X20CrMoWV12-1 are trusted for their high-temperature capabilities in both power plants and heavy machinery.
Conclusion
The stainless steel grades AISI 422, AISI 616, SUH 616, B50A951, 1.4935, and X20CrMoWV12-1 each offer distinct advantages for different applications. From aerospace to power generation, these materials provide exceptional performance under extreme conditions. Understanding their unique properties allows manufacturers to choose the right material for each specific application, ensuring long-term reliability and performance.
Products Form:
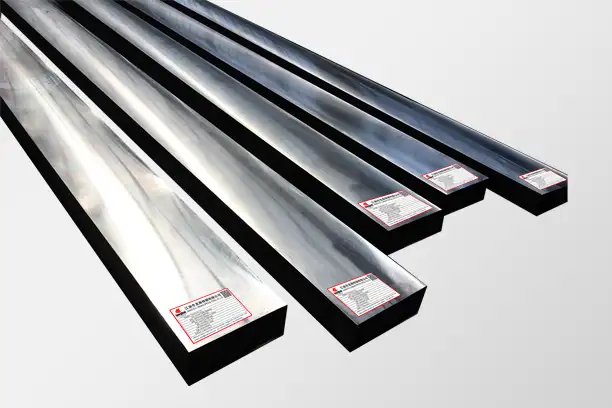
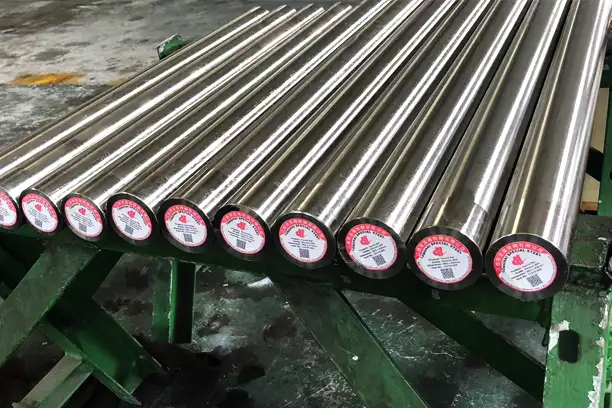
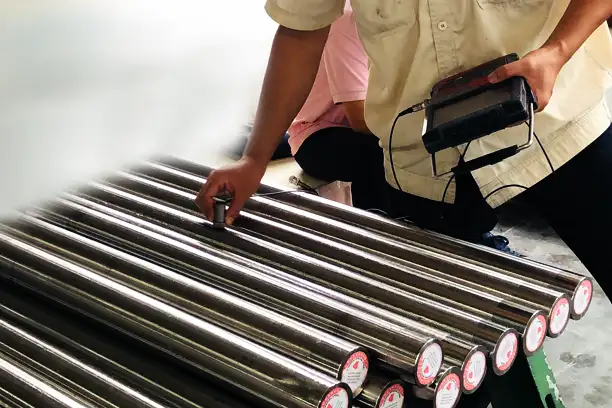
Chemical Composition
Grade | Chemical composition WT % | ||||||||||||||
---|---|---|---|---|---|---|---|---|---|---|---|---|---|---|---|
C | Si | Mn | P | S | Cr | Mo | Ni | V | W | Cu | Sn | Al | Co | Ti | |
Ge Power B50A951 A1 | 0.20-0.25 | 0.20-0.50 | 0.50-1.00 | Max 0.025 | Max 0.015 | 11.00-12.50 | 0.90-1.25 | 0.50-1.00 | 0.20-0.30 | 0.90-1.25 | Max 0.15 | Max 0.02 | Max 0.025 | 0.20 | 0.025 |
Ge Power B50A951 A2 | 0.20-0.25 | 0.20-0.50 | 0.50-1.00 | Max 0.020 | Max 0.010 | 11.00-12.50 | 0.90-1.25 | 0.50-1.00 | 0.20-0.30 | 0.90-1.25 | Max 0.15 | Max 0.02 | Max 0.025 | 0.20 | - |
Ge Power B50A249 S12 | 0.20-0.25 | 0.20-0.50 | 0.50-0.90 | 0.025 | 0.025 | 11-12.50 | 0.9-1.25 | 0.5-1.0 | 0.2-0.3 | 0.9-1.25 | - | 0.02 | 0.025 | 0.20 | 0.05 |
ASME B4B, ASTM Grade B4B | 0.20-0.25 | 0.20-0.50 | 0.50-1.00 | Max 0.025 | Max 0.025 | 11.00-12.50 | 0.90-1.25 | 0.50-1.00 | 0.20-0.30 | 0.90-1.25 | - | Max 0.04 | Max 0.05 | Max 0.050 | |
ASTM A565 616 | 0.20-0.25 | Max 0.50 | 0.50-1.00 | Max 0.025 | Max 0.025 | 11.00-12.50 | 0.90-1.25 | 0.50-1.00 | 0.20-0.30 | 0.90-1.25 | - | - | - | - | - |
EN 1.4935, X20CrMoWV12-1 | 0.17-0.24 | 0.10-0.50 | 0.30-0.80 | Max 0.025 | Max 0.015 | 11.0-12.5 | 0.80-1.20 | 0.3-0.8 | 0.25-0.35 | 0.4-0.6 | - | ||||
JIS SUH 616 | 0.20-0.25 | Max 0.50 | 0.50-1.00 | Max 0.040 | Max 0.03 | 11.0-13.0 | 0.75-1.25 | 0.5-1.0 | 0.2-0.3 | 0.75-1.25 | Max 0.3 | ||||
ASTM AISI 422, AISI 616, S42200 | 0.20-0.25 | Max 0.75 | Max 1.00 | Max 0.040 | Max 0.03 | 11.0-12.5 | 0.75-1.25 | 0.5-1.0 | 0.15-0.30 | 0.75-1.25 | Max 0.5 |
Mechanical Properties
Type 422 Mechanical properties acc. to GE B50A951
- Type 422 Class A1, A2, A4
- Tensile strength KSI(MPa): Min 140(965)
- Yield Strength 0.02%, Offset KSI(MPa): Min 90(620) *
- Elong. In 2": Min 13 %
- RA: Min 35%
- Brinell Hardness, 3000Kg laod: 285-331
- Kv, Min at R.T. ft-lb(J): 10(13.36)
- Type 422 Class A3
- Tensile strength KSI(MPa): Min 110(759)
- Yield Strength 0.02%, Offset KSI(MPa): Min 80(555) *
- Elong. In 2": Min 18 %
- RA: Min 50%
- Brinell Hardness, 3000Kg laod: 223-269
- Kv, Min at R.T. ft-lb(J): 25(33.90)
Tensile Requirements (B50A249B Only)
- Tensile Strength, psi, min. 140,000
- Yield Strength, psi, 0.02%, min. 90,000
- Elongation, % in 2 inches, min. 12
- Reduction of Area, %, min. 25
- Charpy V-Notch Impact Energy Requirements (B50A249B Only)
- Hardness Requirements
Two Charpy V-Notch Impact energy tests shall be conducted at room temperature (70F +/-10F) and have following properties:
Standard Charpy V-Notch Impact, ft-lb, min. 10
Two Brinell Hardness measurements shall be taken at the 0-degree and 180 Degree locations on one end and at the 90-degree and 270-degree locations on the opposite end of each forging. The measurements shall be taken at each end, on either the end face or a radial face in close proximity to the end. All measurements must meet the following requirements:
Brinell Hardness Number, 3000 kg load 290-332
Stress Rupture Requirements (B50A249B Only)
Smooth bar stress rupture tests shall be conducted on each forging or each heat treated forging length. The test may be discontinued after the minimum requirement for time to rupture has been exceeded. The test must meet the following requirements:
- Temperature (Degree F): 1200
- Stress (psi): 26,000
- Min. Time to Rupture (hrs.): 25
1.4935 Mechanical properties acc. to EN 10302
- +QT700
- Tensile strength KSI(MPa): 700 to 850
- Yield Strength 0.02%, Offset KSI(MPa): Min 500
- A5 15%
- +QT800
- Tensile strength KSI(MPa): 800 to 950
- Yield Strength 0.02%, Offset KSI(MPa): Min 600
- A5 14%
Grade B4B Stress Rupture
- Test Method: ASTM E139
- Temperature: 650 °C
- Load:200 MPa
- Result: Life = 25 hours,Elongation and Reduction of Area = For information On bar having lowest hardness for each heat lot.
1.4935 QT700 Creep
temperature,(℃) | Time,(h) | 1% Rp1(MPa) | 0.5% Rp0.5(MPa) | 0.2% Rp0.2(MPa) | 0.1% Rp0.1(MPa) | CRS(MPa) |
---|---|---|---|---|---|---|
470 | 10000.0h | 324.0 | - | - | - | 368.0 |
470 | 100000.0h | 260.0 | - | - | - | 309.0 |
470 | 200000.0h | - | - | - | - | 285.0 |
480 | 10000.0h | 299.0 | - | - | - | 345.0 |
480 | 100000.0h | 236.0 | - | - | - | 284.0 |
480 | 200000.0h | - | - | - | - | 262.0 |
490 | 10000.0h | 269.0 | - | - | - | 319.0 |
490 | 100000.0h | 213.0 | - | - | - | 260.0 |
490 | 200000.0h | - | - | - | - | 237.0 |
500 | 10000.0h | 247.0 | - | - | - | 294.0 |
500 | 100000.0h | 190.0 | - | - | - | 235.0 |
500 | 200000.0h | - | - | - | - | 215.0 |
510 | 10000.0h | 227.0 | - | - | - | 274.0 |
510 | 100000.0h | 169.0 | - | - | - | 211.0 |
510 | 200000.0h | - | - | - | - | 191.0 |
520 | 10000.0h | 207.0 | - | - | - | 253.0 |
520 | 100000.0h | 147.0 | - | - | - | 186.0 |
520 | 200000.0h | - | - | - | - | 167.0 |
530 | 10000.0h | 187.0 | - | - | - | 232.0 |
530 | 100000.0h | 130.0 | - | - | - | 167.0 |
530 | 200000.0h | - | - | - | - | 147.0 |
540 | 10000.0h | 170.0 | - | - | - | 213.0 |
540 | 100000.0h | 114.0 | - | - | - | 147.0 |
540 | 200000.0h | - | - | - | - | 128.0 |
550 | 10000.0h | 151.0 | - | - | - | 192.0 |
550 | 100000.0h | 98.0 | - | - | - | 128.0 |
550 | 200000.0h | - | - | - | - | 111.0 |
560 | 10000.0h | 135.0 | - | - | - | 173.0 |
560 | 100000.0h | 85.0 | - | - | - | 112.0 |
560 | 200000.0h | - | - | - | - | 96.0 |
570 | 10000.0h | 118.0 | - | - | - | 154.0 |
570 | 100000.0h | 72.0 | - | - | - | 96.0 |
570 | 200000.0h | - | - | - | - | 81.0 |
580 | 10000.0h | 103.0 | - | - | - | 136.0 |
580 | 100000.0h | 61.0 | - | - | - | 82.0 |
580 | 200000.0h | - | - | - | - | 68.0 |
590 | 10000.0h | 90.0 | - | - | - | 119.0 |
590 | 100000.0h | 52.0 | - | - | - | 70.0 |
590 | 200000.0h | - | - | - | - | 58.0 |
600 | 10000.0h | 75.0 | - | - | - | 101.0 |
600 | 100000.0h | 43.0 | - | - | - | 59.0 |
600 | 200000.0h | - | - | - | - | 48.0 |
610 | 10000.0h | 64.0 | - | - | - | 87.0 |
610 | 100000.0h | 36.0 | - | - | - | 50.0 |
610 | 200000.0h | - | - | - | - | 40.0 |
620 | 10000.0h | 53.0 | - | - | - | 73.0 |
620 | 100000.0h | 30.0 | - | - | - | 42.0 |
620 | 200000.0h | - | - | - | - | 33.0 |
630 | 10000.0h | 44.0 | - | - | - | 60.0 |
630 | 100000.0h | 25.0 | - | - | - | 34.0 |
630 | 200000.0h | - | - | - | - | 27.0 |
640 | 10000.0h | 36.0 | - | - | - | 49.0 |
640 | 100000.0h | 20.0 | - | - | - | 28.0 |
640 | 200000.0h | - | - | - | - | 22.0 |
650 | 10000.0h | 29.0 | - | - | - | 40.0 |
650 | 100000.0h | 17.0 | - | - | - | 23.0 |
650 | 200000.0h | - | - | - | - | 18.0 |
Physical Properties
Density: 7.7 g/cm3
Linear expansion coefficient: 10.5-12.5 *10-6m/(m*K)
Thermal conductivity: 24 W/(m*K)
Specific heat capacity: 460 J/(kg*K)
Young's modulus: 216 GPa
Electrical resistivity: 0.6 µΩ*m
Tensile strength Rm: > 600 MPa
Creep limit for max elongation 0.2% Rp0.2: Min 800 MPa
Creep-rupture strength Ru: Min 275 MPa; 500°C; 100000h
Heat Treatment
Austenitization-Material shall be heat treatedto1875-1925F and held at temperature for a sufficient time to assure uniform temperature within the load and each part thereof.
Quenching -Material shall be quenched to a temperature below 600℉ and then cooled to a temperature below theM(approximately 150℉) to assure complete transformation.
B50A951 A1-Material shall be oil quenched.Use of air quenching is prohibited.
B50A951 A2, A3, A4-Material shall be quenched in oil or rapidly moving air.
Tempering-Material shall be uniformly heated to the tempering temperature of 1150F° minimum.
Heat treatment for 1.4935
- Quenching: 1020-1070 °C
- Tempering: 680-780 °C
Heat treatment for B50A249 S12
- Austenitization (All Classes)
- Quenching
- B5QA249B
- B50A249C
- Tempering (All Classes)
- Stress Relief Anneal (SRA)
Forging shall be heated slowly to 1875oF- 1925oF and held at temperature approximately 30 minutes per inch of thickness or diameter, to assure uniform temperature within the load and each part thereof.
Each forging shall be oil quenched to a temperature below 600F. The forging shall then be cooled to a temperature below the Mf temperature (approximately 300F) to assure complete transformation. GE Test Method E50A209 is to be used as a guide for selecting adequate quenching times. Time of immersion in oil, and the maximum surface temperature of the forging during the first ten minutes after removal from the oil shall be reported.
Forging shall be forced air quenched to a temperature below the Mf temperature (approximately 300F) to assure complete transformation.
Forging shall be double tempered. The first temper shall be at 110OF minimum. The second temper shall be at 11 50F minimum. The forging shall be held at the temperature for one (1) hour per inch of maximum thickness or diameter during the tempering cycle and then cooled uniformly to room temperature.
When a stress relief heat treatment is performed, the forging shall be stress relieved at a temperature 50F below the final tempering temperature and shall be still air or furnace cooled.
Thermal Properties
1.4935 High Temperature acc. to EN 10302
- +QT700
- Temp 50 °C - > 465 MPa
- Temp 100 °C - > 460 MPa
- Temp 150 °C - > 445 MPa
- Temp 200 °C - > 430 MPa
- Temp 250 °C - > 415 MPa
- Temp 300 °C - > 390 MPa
- Temp 350 °C - > 380 MPa
- Temp 400 °C - > 360 MPa
- Temp 450 °C - > 330 MPa
- Temp 500 °C - > 290 MPa
- Temp 550 °C - > 250 MPa
High Temperature
- +QT800
- Temp 50 °C - > 585 MPa
- Temp100 °C - > 560 MPa
- Temp 150 °C - > 545 MPa
- Temp 200 °C - > 530 MPa
- Temp 250 °C - > 505 MPa
- Temp 300 °C - > 480 MPa
- Temp 350 °C - > 450 MPa
- Temp 400 °C - > 420 MPa
- Temp 450 °C - > 380 MPa
- Temp 500 °C - > 335 MPa
- Temp 550 °C - > 280 MPa
High Temperature
Welding Properties
welding of this material is not straightfor- ward owing to its crack sensitivity.
Machining Properties
Machining
What is AISI 422, S42200, 616 equivalent to?
AISI 422, AISI 616, S42200, 1.4935, X22CrMoWV12-1, SUH616, 20VNiWMoCr120, ,EW 4935, T502, 56B.I., DE 4935, HWMoV3, Grade 616, B50A951 A1, A2, A3, A4, HT9