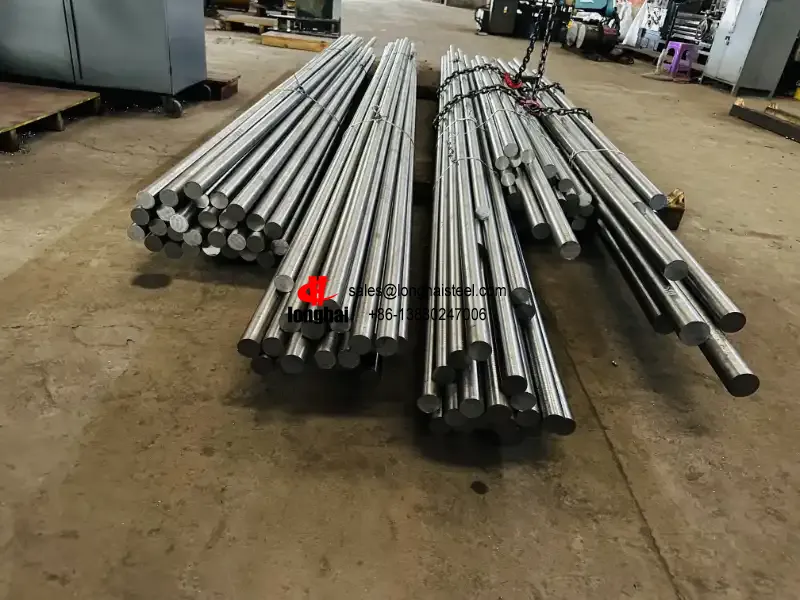
X25CrMnNiN25-9-7 is a nitrogen-enhanced austenitic stainless steel known for its high strength, excellent corrosion resistance, and good toughness even at elevated temperatures. It is part of the EN standard stainless steel grades and is widely used in demanding industrial applications requiring durability and performance under stress.
- Heat Treatment
- Thermal Properties
- Welding
- Machining
- Similar or equivalents steel grade
What is grade steel?
X25CrMnNiN25-9-7 is suitable for:
1. Chemical and Petrochemical Industry: Storage tanks, pipelines, and heat exchangers.
2. Food Processing Equipment: Components exposed to corrosive cleaning agents.
3. Marine Applications: Structural components in sal
Chemical Composition
Element | Min | Max | Similar | Note |
---|---|---|---|---|
Si | - | 1.0000 | - | |
S | - | 0.0150 | - | |
P | - | 0.0450 | - | |
Ni | 6.0000 | 8.0000 | - | |
N | 0.2000 | 0.4000 | - | |
Mn | 8.0000 | 10.0000 | - | |
Cr | 24.0000 | 26.0000 | - | |
C | 0.2000 | 0.3000 | - |
Mechanical Properties
Yield Strength: ~400–450 MPa
Ultimate Tensile Strength (UTS): ~700–800 MPa
Elongation at Break: ~40%
Hardness: Approximately 200–250 HB
Physical Properties
X25CrMnNiN25-9-7 is a high-nitrogen austenitic stainless steel, and its physical properties reflect its robust composition, making it suitable for demanding applications. Below are the key physical characteristics:
Density: Value: ~7.8 g/cm³ (7800 kg/m³)
This density is typical of austenitic stainless steels, ensuring good strength-to-weight ratio for structural applications.
Thermal Conductivity: Value: ~15–20 W/m·K (at room temperature, ~20°C or 68°F)
Moderate thermal conductivity compared to other stainless steels, due to its austenitic microstructure and nitrogen content.
Suitable for environments where heat transfer is not the primary concern.
Specific Heat Capacity: Value: ~500 J/kg·K (at room temperature)
Thermal Expansion: Coefficient: ~16–17 × 10⁻⁶ /K (in the range of 20–300°C or 68–572°F)
Electrical Resistivity: Value: ~0.8–0.9 μΩ·m (at room temperature)
Modulus of Elasticity: Value: ~200 GPa (29 × 10⁶ psi)
Melting Range: Range: ~1375–1450°C (2507–2642°F)
Heat Treatment
X25CrMnNiN25-9-7 is a high-nitrogen austenitic stainless steel known for its excellent strength, toughness, and corrosion resistance. The heat treatment of this grade aims to optimize its mechanical properties and corrosion resistance. Below are the typical heat treatment steps:
Solution Annealing
- Temperature Range: 1050–1100°C (1922–2012°F)
- Soaking Time: Based on the thickness of the material, generally 1–2 minutes per mm, with a minimum of 30 minutes.
- Cooling Method: Rapid water quenching or air cooling to avoid carbide precipitation.
Note: Rapid cooling is crucial to prevent sensitization (chromium carbide precipitation leading to intergranular corrosion).
Stress Relieving
Stress relieving helps to reduce residual stresses from machining or cold working without significantly altering the material’s microstructure.
- Temperature Range: 300–400°C (572–752°F)
- Soaking Time: 1–2 hours.
- Cooling Method: Slow air cooling.
Note: While stress relieving does not eliminate all residual stress, it reduces the risk of stress-corrosion cracking.
Post-Weld Heat Treatment (PWHT)
Post-weld heat treatment is essential for restoring the material’s properties after welding, especially for components used in high-stress environments.
- Temperature Range: 1050–1100°C (1922–2012°F) for full solution annealing.
- Soaking Time: Adjust based on the thickness of the weld and the component.
- Cooling Method: Rapid water quenching or air cooling.
Note: PWHT ensures the weld heat-affected zone (HAZ) regains its uniform mechanical and corrosion-resistant properties.
Welding Properties
Welding Techniques: TIG (GTAW) or MIG (GMAW) is preferred.
Filler Metal: Use a matching nitrogen-enhanced filler (e.g., ER2594 or similar) to retain the alloy’s properties.
Preheat: Not typically required, but for thick sections, mild preheating (~100–150°C) may improve outcomes.
Post-Weld Treatment: Annealing
Machining Properties
Work-Hardening Tendency: Due to its high nitrogen content, X25CrMnNiN25-9-7 is prone to work hardening. Use sharp tools and minimize tool pressure.
Cutting Tools: Carbide tools with high wear resistance are recommended.
Cutting Speeds: Use moderate speeds and avoid excessive heat to prevent hardening.
Coolants: Apply ample coolant to maintain stability and reduce tool wear.
Feeds: Moderate feed rates to avoid excessive strain and ensure a clean cut.