Steel X10CrNiMoV12-2-2 Forged Bars for Steam Turbine Blades
January 16,2023
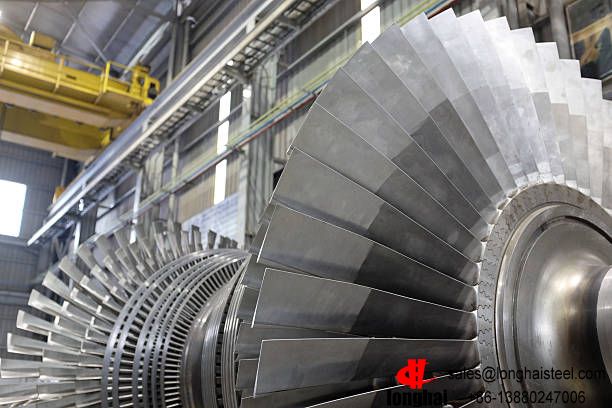
Abstract
Steel X10CrNiMoV12-2-2(%:0.08~0.13C,11.4~12.5Cr,2.2~2.8Ni,1.6~1.8Mo,0.25~0.40V,0.020~0.040N) melted by 20 t EAF-AOD-LF process cast toΦ490 mm electrode,eleetroslag-remelted toΦ600 mm ingot and forged toΦ180~240 mm bar products.Examination results show that the residual deleterious element con- tent is 0.002%Sb,0.010%As and 0.010%Sn;the rating of inclusions,grain size,mechanical properties,fracture ap- pearance transition temperature(FATT),percentage of intercrystalline fracture and freeδferrite content in steel all meet the requirement of technical standard.
X10CrNiMoV12-2-2 alloy is a Cr-Ni-Mo-V-N type supercritical, ultra-supercritical blade steel [1,2]. X10CrNiMoV12-2-2 alloy steel is similar to GX-8 and 1Cr12Ni3MoVN steel, and its main features are: (1) It has an obvious temper brittle zone at 450-550 °C. (2) It has good comprehensive performance: plasticity, fatigue performance, durability, creep performance, corrosion resistance, weldability and formability. (3) Considering the metallographic structure, the steel is already on the martensite-ferrite boundary. Therefore, the increase of any ferrite-forming elements will obviously affect the ferrite content in the steel, which will affect the mechanical properties of the steel. produce adverse effects.
Development process and process
The production process of steel for forging rods: 20 t electric arc furnace smelting alloy, after AOD and LF, casting into Φ490 mm×3 250 mm electrode; after surface finishing, electroslag remelting into Φ600 mm×2 000 mm ingot; finishing After processing and taking chemical analysis samples, use 4000T fast forging/2000T fast forging to process the required Φ180-240 mm finished forged rods; after annealing, perform ultrasonic flaw detection, and take samples to test performance.
1.1 Smelting of electric arc furnace and electroslag furnace
The chemical composition of the X10CrNiMoV12-2-2 alloy is shown in Table 1. During electric arc furnace smelting, due to the requirement of low Si content in the alloy, the electric arc furnace smelting process must use A1 powder for deoxidation; the steel contains N and the control of Mn content in the steel must be taken into account. Burning loss to ensure its content requirements; the purity requirements of this steel are strict, and special smelting technology should be adopted during steelmaking to facilitate the floating of inclusions and ensure the purity requirements.
During electroslag remelting, the burning loss of beneficial elements should be reduced and the content of residual elements such as Ti and Al should be well controlled to ensure that the alloy has an ideal structure.
Table 1 Requirement of chemical composition and analysis of electrode and ESR ingot of steel X10CrNiMoV12-2-2/%
The electrode composition and electroslag ingot composition of X10CrNiMoV12-2-2 steel smelted by electric arc furnace are shown in Table 1
1.2 Forging
The ingots and billets of the developed steel for forging rods are all heated in a chamber furnace at a heating temperature of 1150°C. This steel has high thermoplastic deformation capacity at high temperature and is easy to process. However, in order to avoid coarse grains, a specific heating forging process is still required, and the forging stop temperature should not be too high. When the steel ingot is forged, there should be enough cut off at both ends to ensure that the forging billet has no defects such as shrinkage cavity, slag inclusion, looseness, and severe segregation.
Test results of test specimens of steel for wrought bars
The sample size of the developed steel for forging bar is 90mm × 90mm
2.1 Lateral low magnification and fracture
The transverse low magnification and fracture detection results of steel samples for forging bars developed in No. 8 furnace are general porosity of 0.5 grade, central porosity of 0 grade, ingot shape segregation of 0.5 grade, and the fracture inspection is qualified.
2.2 Purity
The purity test results of the developed steel for forging bars are shown in Table 2. It can be seen from the results in Table 2 that the purity of the developed steel for forging bars can fully meet the technical standards of Siemens, which is comparable to foreign products.
2.3 Flaw detection inspection
Ultrasonic testing is carried out on the developed steel products for forging rods according to the relevant standards, and the evaluation standard is grade A (Φ1.2 mm hole). The developed products (Φ100~240 mm round rods) have no damage wave in test results, and all are qualified.
2.4 Mechanical properties and structure
The sample blanks of the developed steel for electric arc furnace + electroslag forging rods are processed into standard samples after heat treatment according to a certain heat treatment process system. MPa, A 16%~20%, Z 65.5%~68.5%, HB 321; transverse Rm 1 050~1 070 MPa, Rp0.2890~900 MPa, A 19.5%~20%, Z 64.5%~66%, HB 298-383.
The mechanical properties of the steel for forging bars developed in this paper have fully reached the technical performance indicators of X10CrNiMoV12-2-2 steel for forging bars.
2.5 FATT test and intergranular fracture percentage test
According to the brittle transition temperature FATT and intergranular fracture percentage test standard and test method, the FATT and intergranular fracture percentage of the developed alloy were detected. The test results of 8 furnace steels show that the brittle transition temperature FATT of the developed X10CrNiMoV12-2-2 steel is -39.0~-39.5℃, and the percentage of intergranular fracture is ≤10%, which fully reaches the FATT of the X10CrNiMoV12-2-2 steel for forging bars. The technical performance indicators of ≤-35°C and fracture fiber ratio ≤10% meet the performance requirements.
Table 2 Examination results of inclusions and grain size of forged products of steel X10CrNiMoV12-2-2
Charpy V-type impact energy AKV and δ free ferrite
The Charpy V-type impact energy AKV of the developed alloy: 144-192 J in the longitudinal direction and 120-160 J in the transverse direction; the δ free ferrite content is 1%, both of which exceed Siemens X10CrNiMoV12-2-2 steel AKV≥50 J and δ free iron The technical performance index of element body ≤5%.