Metallurgical Analysis and Simulation of a Service-Fractured Compressor Blade Made of ASTM S45000 Alloy
February 23,2023
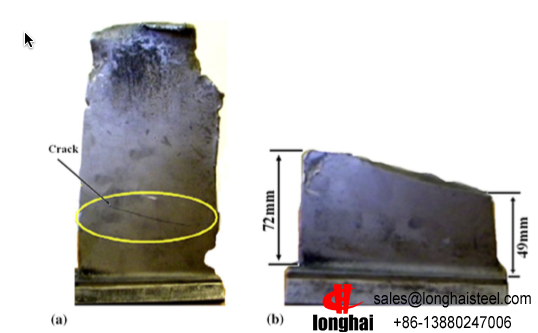
Blades are key components of gas turbine compressors which are frequently subjected to centrifugal and vibratory loads.These cyclic loadings result in degradation of physical and mechanical properties of the blades. Moreover, the blades operate at high temperature and in aggressive environments which makes monitoring their properties hard, and as a consequence their useful life service is limited. In order to prevent early and sudden failure of compressor blades, it seems rational to f i nd out the reason for limited service life of the blades. Experi-mental and metallurgical investigations on a service-fractured compressor blade combined with blade simula-tion and stress analysis resulted in calculation of cycles for fatigue crack initiation and propagation and understanding of the sudden failure ofthe blade made of Custom 450 alloy in this case study during service.
Introduction
Turbo machines have been widely used in heavy industries such as aviation, energy, oil ref i ning, petrochemical, coal chemical, natural gas transportation, metallurgy and other important areas. Compressor blades are required to resist high mechanical loads imposed by high rotational speed in the form of large centrifugal loads and aerodynamic forces applied as a function of pressure rise through each stage of the compressor section. The failures ofblades as the key components ofturbo machines resultinsignif i canteconomic losses. The common modes off ailure in compressor bladesis fatigue failure as a result of improper assembly, fretting, mechanical abnormalities induced during manufacturing or by foreign and internal object damage during engine opera- tion. Corrosion pits facilitate fatigue crack initiation andpropagation. Researchonbladefailures, especially on fatigue fracture as the main failure mode, is necessary for designing, manufacturing and application of compressor blades. Environmental factors combined with external loads on the blades lead to their early failure. The fatigue life ofa material with different crack sizes can be calculated by the models with the parameters under operational conditions. In the prediction of fatigue life of compressor blades, the operational conditions are poorly monitored in the research. However, those parameters can be simulated effectively by f i nite element analysis. The objective of the present study is to investigate the reason forsudden and early failure of a gas compressor blade working about 34,000 h in a sea water environment by considering metallurgical factors and 3D f i nite element simulation. Materials and Methods The height, width and thickness of the blade studied in this research are 216, 140 and 2 mm, respectively. Chemical analysis of the blade material was carried out by emission spectrometry.Table 1 presentsthechemical analysis results which comply with UNS S45000 require- mentsforcompressorblades.Themetallographic specimens were ground with 120–2000 mesh sand paper, and the cross sections were polished by diamond paste and solvent. The specimens were etched with a solution of