STAINLESS STEEL BAR AND FORGING Cr-Ni-Cu-Cb-Fe ALLOY - GTD-450
November 01,2024
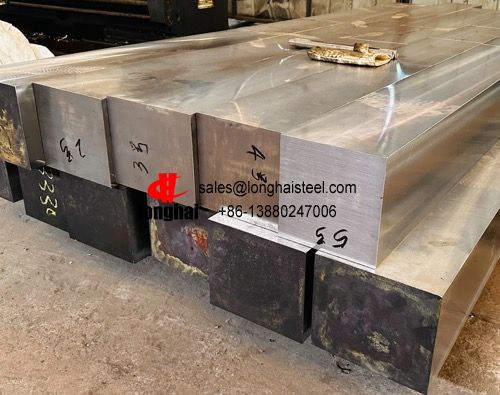
STAINLESS STEEL BAR AND FORGING (Cr-Ni-Cu-Cb-Fe ALLOY - GTD-450)
1. SCOPE
1.1 General Electric Material B50A789 identifies a Chromium-Nickel-Copper-Columbium-Iron alloy steel, as forged, extruded or machined, from bar or billet, for compressor blading and steam turbine buckets.
1.2 This specification contains the following classes:
- B50A789A Hot rolled, overaged
- B50A789B Solution Treated
- B50A789C Obsolete - Do Not Use
- B50A789D Obsolete - Do Not Use
- B50A789E Solution treated and aged, 1070°F
- B50A789F UT inspection, solution treated and aged, 1070°F
- B50A789G Solution treated and aged, 900°F min.
- B50A789H Solution treated and aged, 1100°F
1.3 Raw material (bar) produced to B50A789 must meet the applicable requirements set forth in P14A-AL-0208 and this specification.
1.4 Raw material (bar) produced to B50A789, Class A and Class B, which will be subsequently formed by forging and/or extrusion processing, shall be supplied to a maximum hardness and heat capability requirements only.
1.5 Compressor Blades, Vanes and Variable Inlet Guide Vanes (forged, extruded and/or machined) produced to B50A789 must also meet the applicable requirements set forth in process specification P3C-AG60.
1.6 All questions or requests for additional information shall be submitted to GE Power for clarification. Conflicts between applicable Specifications or drawings shall be submitted to GE Power for resolution by engineering.
1.7 Bucket forgings produced to B50A789, Class G must meet the applicable requirements set forth in P14A-AL-0211, “Bucket/Partition Forgings - General Requirements”.
APPLICABLE DOCUMENTS
2.1 The following documents shall form a part of this specification. The latest issue shall apply.
2.1.1 General Electric Company
- P3C-AG60: Compressor Blades, Vanes and Variable Inlet Guide Vanes
- P10A-AG2: Heat Treat, Process Control
- P28A-AL-0002: Supplier Quality Requirements
- P14A-AL-0208: General Requirements - Hot and Cold Finished Steel Bar Products
- P14A-AL-0211: Bucket/Partition Forgings - General Requirements
- P23E-AL-0001: Procedure for Color Coding of Raw Material
2.1.2 Aerospace Material Specification
- AMS-2315: Determination of Delta Ferrite Content
- AMS-STD-2154: Inspection, Ultrasonic, Wrought Metals, Processes For
2.1.3 American Society for Testing and Materials
- ASTM E45: Standard Test Methods for Determining the Inclusion Content of Steel
- ASTM E112: Standard Test Methods for Determining Average Grain Size
- ASTM A751: Standard Test Methods, Practices, and Terminology for Chemical Analysis of Steel Products
3. REQUIREMENTS
3.1 Qualification is required in accordance with the requirements of P3C-AG60, P14A-AL-0208 or P14A-AL-0211, as applicable. Documented acknowledgment of such Qualification from MPE is required prior to general production of raw material or parts, as applicable
3.2 Process
3.2.1 The steel shall be made using the basic electric furnace process with either the Electro-Slag Re-Melt (ESR) or Vacuum-Arc-Re-Melt (VAR) process.
3.3 Chemical Composition (%) (All Material Classes)
Element | Class A, B, E, F and H | Class G |
Carbon | 0.025 - 0.045 | 0.03 - 0.05 |
Manganese, max. | 1.0 | 0.3 - 0.8 |
Silicon, max. | 1.0 | 0.2 - 0.5 |
Phosphorus, max. | 0.025 | 0.020 |
Sulfur, max. | 0.005 | 0.005 |
Chromium | 14.0 - 16.0 | 14.0 - 16.0 |
Nickel | 6.0 - 7.0 | 6.2 - 6.8 |
Molybdenum | 0.5 - 1.0 | 0.6 - 1.0 |
Copper | 1.25 - 1.75 | 1.35 - 1.75 |
Columbium (Niobium) | 0.40 - 0.75 | 8 x C - 15 x C |
Vanadium, max. | 0.10 | 0.10 |
Nitrogen, max. | 0.030 | 0.030 |
Balance - Fe |
Residuals
Element | Max. Value |
Silver | 0.005 |
Lead | 0.005 |
Tin | 0.10 |
Aluminum | 0.05 |
3.3.1
NOTE: Chemical Composition is required for re-melt material (ESR and VAR, as approved) from each re-melted ingot or product thereof involved in the Purchase Order. Refer to ASTM A751 for chemistry analysis methods.
NOTE: Chemical segregation, such as that characterized by banding in the axial direction of bars made to the requirements of this specification, must be limited in severity so as not to interfere with Magnetic Particle Inspection (MPI) of parts or produce unacc eptable indications during MPI of parts made from this material. Indications resulting from chemical segregation must not obscure indications in excess of the size limits specified in P3C-AG60.
3.4 Heat Treatment
Ingot Homogenization
For Compressor Blading Applications - Ingots shall be homogenized at 2100 - 2200°F for a minimum of 12 hours prior to forging or bar process.
For Applications Other Than Compressor Blading - Alternate thermal cycles for homogenization may be acceptable but must be included in an approved Manufacturing Process Plan.
Material shall be heat treated as follows:
- B50A789A - Hot rolled; overaged 1150°F ± 25°F, and prepared with no defects detrimental to forging/extruding.
- B50A789B - Solution treated, 1900°F ± 25°F, or water quench and prepared with no defects detrimental to forging/extruding.
- B50A789E - Solution treated, 1900°F ± 25°F, forced air cool or water quench and aged at 1070°F ± 10°F.
- B50A789F - Same as B50A789E.
- B50A789G - Forged, solution treated, 1900°F ± 25°F, forced air cool, oil quench and aged at 900°F min. ± 8°F (5°C).
- B50A789H - Forged, solution treated, 1900°F ± 25°F, forced air cool and aged at 1100°F ± 10°F.
For Classes A, B, E, F and H
3.4.1 Solution treatment time shall be 45 minutes minimum to 2.5 hours maximum. Aging time at temperature shall be 4.0 hours minimum followed by air cooling.
3.4.2 B50A789H forgings shall be suspended in furnace during the solution and aging treatments.
3.4.3 If any straightening or cold-pressing operation is performed the forgings and bars shall be stress relief annealed. Straightening operation shall be performed after solution and before aging heat treatments.
For Class G
- 3.4.4 Solution treatment time shall be 1 hour minimum to 2 hours maximum at solution temperature. Aging time at temperature shall be 4.0 hours minimum followed by air-cooling.
3.4.5 all straightening operations are to be performed before the final aging treatment.
For All Classes
3.4.6 Temperatures refer to metal temperature at center of heaviest section. Age temperature shall be determined by load thermocouples. All times refer to time at temperature for center of heaviest section. Heat treatment is to be conducted in accordance w ith P10A-AG2, or Purchaser approved equivalent.
3.5 Mechanical Test Requirements
3.5.1 Longitudinal Room Temperature Tensile/Hardness/Impact Properties
Classes E & F | Class H | Class G | |
Tensile Strength (ksi), min. | 146 -175 | 140 -175 | 180-195 |
Yield Strength - 0.2% Offset (ksi), min. | 132 | 120 | - |
Yield Strength - 0.02% Offset (ksi), min. | - | - | 140 |
Elongation in 4D, %, min | 16 | 16 | 13 |
Reduction of Area, %, min. | 50 | 50 | 45 |
Hardness: Brinell, 3000 kg Load | 302-363 | 302-363 | 380-415 |
Impact, Room Temp., Charpy V-Notch (Ft.-Lbs.), min. | 50 | 50 | 40 |
3.5.2 Short Transverse
Class E, F and H | Class G | |
Tensile Strength (ksi), min. | 140-175 | 180 |
Yield Strength - 0.2% Offset. (ksi), min. | 120 | - |
Elongation in 4D - %, min | 16 | 5 |
Reduction of Area, %, min | 50 | - |
Impact, Room Temp., Charpy V-Notch (Ft.-Lbs.), min. | 40 | - |
3.5.3 If standard length Charpy 2.165’’ [55mm] specimens cannot be taken from the short transverse direction the specimens shall be taken from the long transverse direction. Transverse Charpy testing for bar diameters <2.56’’ [65 mm] not required. If stand ard size tensile cannot be machined test bar size, locations and quantity shall be as agreed upon by supplier and purchaser.
3.5.4 If standard size tensile (.250 inch [6.25 mm] dia. x 1.000 inch [25.0 mm] gage length) specimens cannot be taken from the short transverse direction the specimen size and location shall be as agreed upon by supplier and purchaser.
3.5.5 NOTE: Material supplied for subsequent forming by forging and/or extrusion (B50A789 - Class A) shall meet the requirements for capability (Ref. Para. 3.5.5) and the following:
3.5.5.1 Hardness
Brinell, 3000 kg load Max., 311
3.5.6 Material supplied for subsequent forming by forging and/or extrusion (B50A789 Class A or Class B) must conform to heat capability in accordance with P14A-AL-0208, to the requirements of B50A789 Class E material, as set forth in this specification (se ctions. 3.5.1, 3.5.2 and 3.6).
3.5.7 NOTE: When subjected to Brinell hardness testing, B50A789 experiences a martensitic transformation due to the cold work produced during testing. Conventional steel hardness conversion tables do not apply to this material. Methods other than Brinell h ardness testing shall be approved by MPE.
3.6 Metallography (B50A789 Class E, F, and H Only) - For Class E, F, and H material, samples taken in accordance with P14A-AL-0208.
3.6.1 An average prior austenitic grain size of ASTM No. 5, or finer with grains as large as ASTM 3 as long as they are surrounded by finer grains. (Ref. P14A-AL-0208 - Re. ASTM E112).
3.6.2 A maximum of two (2) percent delta ferrite (Ref. P14A-AL-0208 - Ref. AMS-2315).
3.6.3 A cleanliness requirement of ASTM E45, Method D, maximum allowable inclusion rating number of 2 for thin inclusion widths and 1 1/2 for heavy inclusion widths
3.6.4 Reference P3C-AG60 for forging/extrusion and finished blade metallography requirements.
3.7 Metallography (B50A789G Only) - For Class G material, samples taken in accordance with P14A-AL-0211 shall exhibit the following:
3.7.1 An average prior austenitic grain size of ASTM No. 6, or finer (Ref. P14A-AL-0208 - Re. ASTM E112).
3.7.2 A maximum of 0.5 percent delta ferrite (Ref. P14A-AL-0208 - Ref. AMS-2315).
3.7.3 A cleanliness requirement of ASTM E45, Method D, maximum allowable inclusion rating number of 2 for thin inclusion widths and 1 1/2 for heavy inclusion widths
3.7.4 Reference P14A-AL-0211 for forging/extrusion and finished blade metallography requirements.
- QUALITY ASSURANCE PROVISIONS
4.1 Ultrasonic Test (B50A789 Class F and G Only)
4.1.1 Bar stock shall be inspected to the requirements of AMS-STD-2154 Class AA as defined on the part drawing. This inspection is to be performed on the bar stock prior to heat treatment.
4.2 Mechanical Tests (B50A789 Class E, F, G and H Only)
4.2.1 Mechanical property tests and test locations shall be in accordance with the requirements of P3C-AG60, P14A-AL-0208, or P14A-AL-0211 whichever is applicable.
4.3 Dimensions and Tolerances - Shall be in accordance with P3C-AG60, P14A-AL-0208 or P14A-AL-0211, as applicable.
4.4 Certification - Is required in accordance with P3C-AG60, P14A-AL-0208 or P14A-AL-0211, as applicable.
4.4.1 Report all heat treatment times and temperatures, including any re-treatment operations.
4.4.2 NOTE: Certification must clearly indicate all material supplied with capability requirement.
4.4.3 NOTE: Parts (extrusions/forgings/machined) manufactured to P3C-AG60 must also incorporate the test sampling plans and certification requirements of P3C-AG60.
- PREPARATION FOR DELIVERY
5.1 Parts - All compressor blades, vanes and variable inlet guide vanes shall be identified, packaged and shipped in accordance with the requirements of P3C-AG60.
5.2 Bar
5.2.1 Each bar shall be identified on one (1) end with the heat number, by metal stamping in accordance with P14A-AL-0208.
5.2.2 Bars shipped directly to a PGE manufacturing facility, other than the Naval and Drive Turbine Systems plant, must be color coded in accordance with P14A-AL-0208 (Ref. P23E-AL-0001).
5.3 Steam Turbine Bucket Forgings - Forgings shall be marked and shipped in accordance with the requirements of P14A-AL-0211.