GTD 450 / C450 / UNS S45000 Stainless Steel Overview
November 30,2024
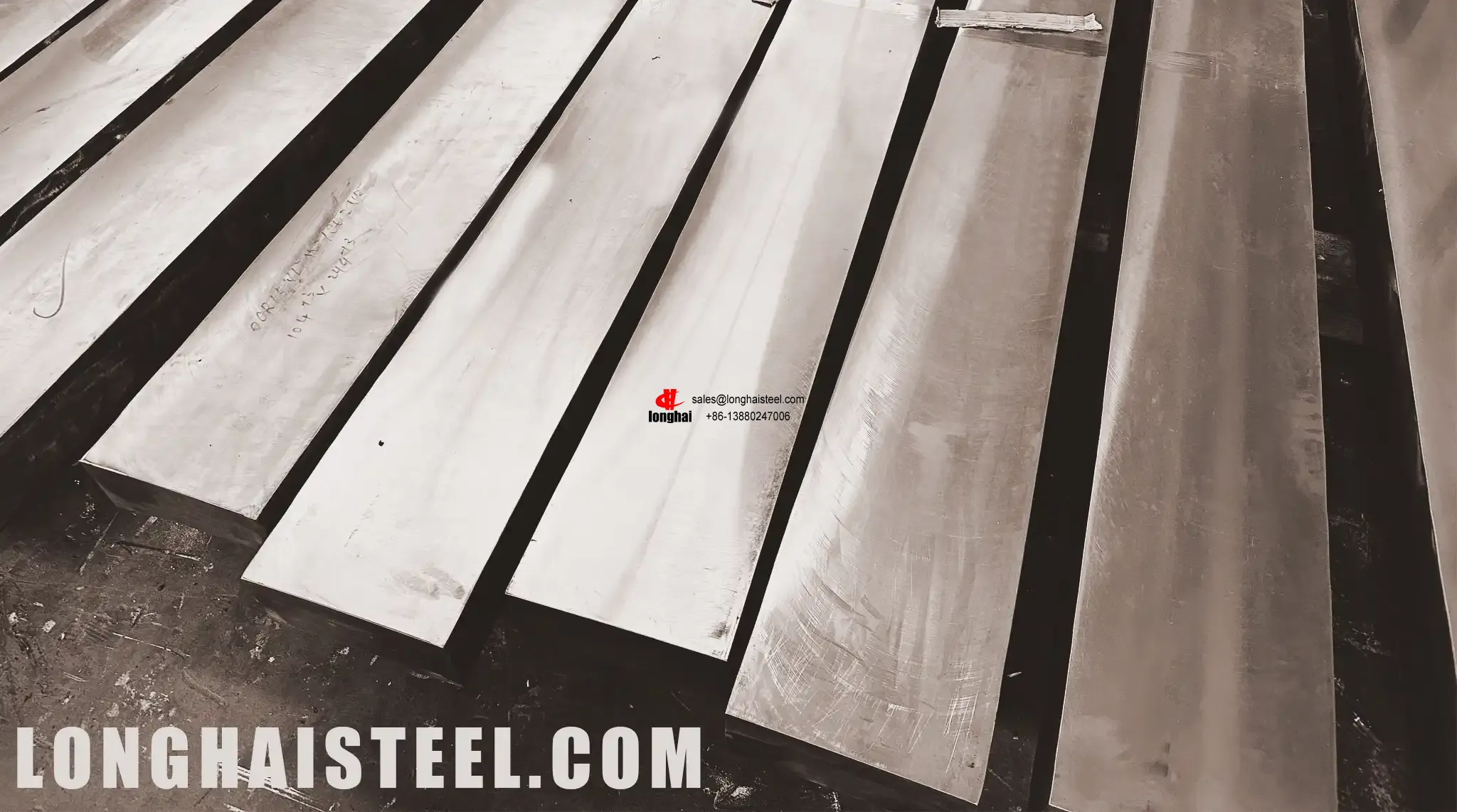
GTD 450 / C450 / UNS S45000 Stainless Steel Overview
GTD 450, also known as C450 or UNS S45000, is a type of martensitic stainless steel renowned for its high strength, excellent corrosion resistance, and exceptional wear properties. This material is often utilized in aerospace, automotive, and industrial applications where a balance of toughness and hardness is required
Key Features and Properties
1. Chemical Composition
- Chromium (Cr): 14.0–16.0%
- Nickel (Ni): 5.0–7.0%
- Molybdenum (Mo): 0.5–1.0%
- Carbon (C): ≤ 0.05%
- Manganese (Mn): ≤ 1.0%
- Silicon (Si): ≤ 1.0%
- Nitrogen (N): ≤ 0.1%
This precise combination ensures good corrosion resistance and mechanical strength.
2. Mechanical Properties
- Ultimate Tensile Strength (UTS): Up to 1700 MPa (varies based on heat treatment)
- Yield Strength: Typically above 1200 MPa
- Hardness: Can achieve HRC 40–45 in hardened condition
- Elongation: Approximately 12–15%
- Solution Annealing: Performed at temperatures around 1025–1050°C (1877–1922°F) followed by air or oil quenching.
- Aging/Tempering: Applied at 480–620°C (896–1148°F) to achieve desired strength and hardness levels.
- Aerospace Components: Landing gear, shafts, and structural elements.
- Automotive Industry: High-performance drive shafts and gears.
- Energy Sector: Gas turbines and compressor blades.
- Industrial Equipment: Wear-resistant components, tools, and dies.
- High strength and toughness.
- Good wear resistance.
- Moderate corrosion resistance for a martensitic steel.
- Requires precise heat treatment for optimal properties.
- Not suitable for highly corrosive environments (e.g., marine).
Cutting Tools
- Use carbide or ceramic tools for optimal performance.
- For rough machining, coated carbide tools (e.g., TiCN or TiAlN coatings) are recommended to enhance tool life and heat resistance.
- Speeds and Feeds
- Maintain low to moderate cutting speeds (approximately 30–50 m/min for carbide tools).
- Use low feed rates for precision and avoid tool chatter, which can affect surface finish.
- Coolants
- Apply flood coolant with high lubricity to dissipate heat and reduce tool wear.
- Water-soluble cutting fluids with anti-corrosion additives are recommended.
- Pre-Hardened Machining
- If machining hardened GTD 450, preheating to ~200°F (93°C) can reduce brittleness during operations.
- Avoid machining fully aged material if possible, as it will be much tougher and wear tools faster.
- Drilling and Tapping
- Use slow spiral carbide drills and ensure sharp cutting edges to avoid heat buildup.
- For tapping, ensure thread-cutting taps are coated and lubricate thoroughly.
- General Advice
- Optimize tool paths to minimize tool entry and exit impacts.
- Regularly monitor tool wear to avoid overloading or work hardening the material.
- Pre-Welding Preparation
- Preheat the material to ~400–600°F (204–316°C) to reduce thermal shock and minimize cracking.
- Ensure the surface is free from contaminants like oils, grease, or oxides.
- Welding Techniques
- Use TIG (GTAW) or MIG (GMAW) welding for precision and controlled heat input.
- Select a matching filler metal with similar composition (e.g., AWS ER630 or ER410).
- Post-Weld Heat Treatment
- Perform immediate post-weld tempering or stress-relieving at 500–700°F (260–371°C) to reduce residual stresses and restore mechanical properties.
- For high-performance applications, full solution annealing followed by tempering may be necessary.
- Avoidance of Cracking
- Slow cooling rates are crucial to prevent hardening cracks.
- Avoid excessive heat input as it can cause distortion and uneven hardness zones.
- Weldability Challenges
- Weld joints in hardened conditions may suffer from loss of toughness.</
3. Corrosion Resistance
GTD 450 provides moderate corrosion resistance, particularly in environments with mild acidity or where exposure to moisture is regular. Its resistance is comparable to other martensitic grades, such as 410 or 420 stainless steel.
4. Heat Treatment
Common Applications
GTD 450 is widely used in the following:
Advantages and Limitations
Advantages
Limitations
Comparison to Similar Grades
Property | UNS S45000 | 410 Stainless Steel | 17-4 PH Stainless Steel |
---|---|---|---|
Corrosion Resistance | Moderate | Moderate | High |
Strength (Hardened) | Higher | Moderate | Comparable |
Heat Treatment Ease | Moderate | Simple | Complex |
Machining Tips
GTD 450 (UNS S45000) is a martensitic stainless steel that poses moderate challenges during machining due to its hardness, especially in the hardened and tempered states. Follow these tips for successful machining:
Weldability
GTD 450 has limited weldability due to its martensitic structure, which is prone to cracking during and after welding. However, welding is feasible with proper precautions: