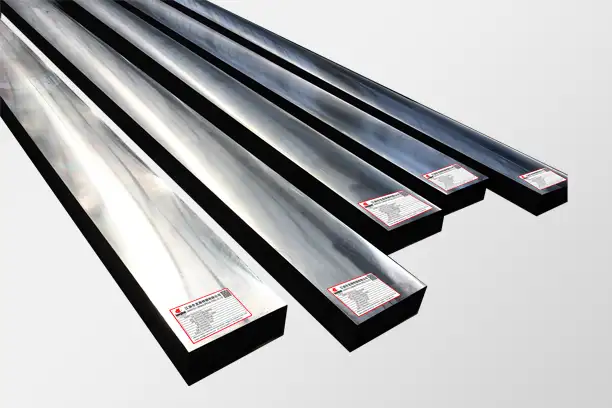
AISI 410, 403 - Construction martensitic stainless chromium steel suitable for the production of Gas turbines, Bolts, screws, bushings and nuts, Petroleum fractionating structures, Shafts, pumps and valves
- Heat Treatment
- Thermal Properties
- Welding
- Machining
- Similar or equivalents steel grade
What is AISI 403 grade steel?
403, 410 stainless steels are general-purpose martensitic stainless steels containing 11.5% chromium, which provide good corrosion resistance properties. However, the corrosion resistance of grade 410 steels can be further enhanced by a series of processes such as hardening, tempering and polishing. quenching and tempering can harden grade 410 steels. 403 martensitic stainless steels are fabricated using techniques that require final heat treatment. These grades are less resistant to corrosion when compared to that of austenitic grades. Their operating temperatures are often affected by their loss of strength at high temperatures, due to over-tempering and loss of ductility at sub-zero temperatures. They are generally used for applications involving mild corrosion, heat resistance and high strength, corrosion resistant chromium martensitic stainless steel used for the production of steam turbine blades, bolts, hydraulic press valves, cracking apparatus, water pump parts, nuts, stainless steel sieves for coal screening and other components working in contact with water and steam
Products Form:
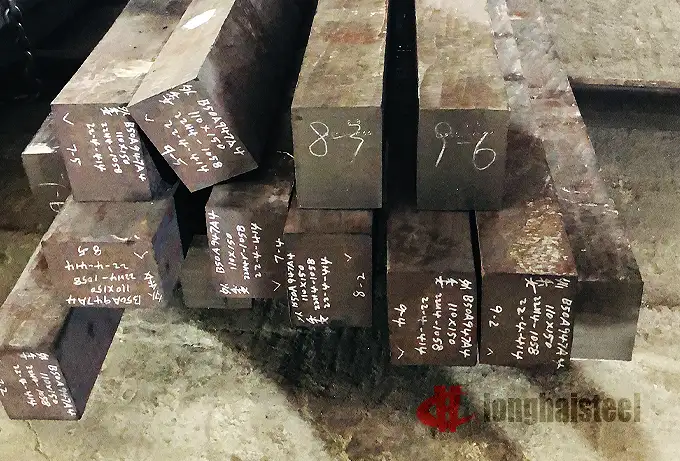

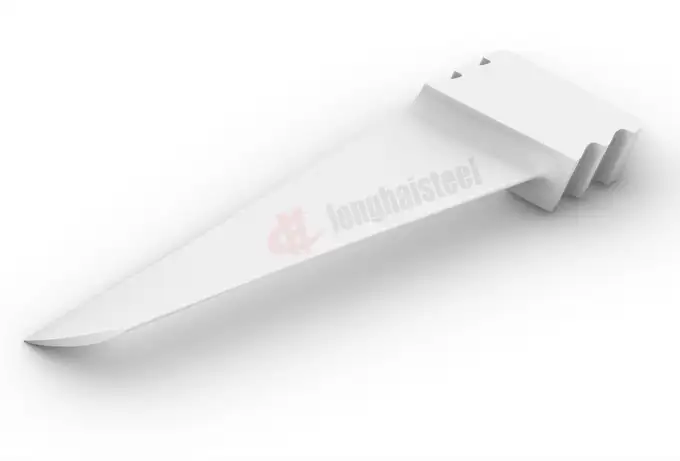
Chemical Composition
Grade | Chemical Composition WT % | |||||||
---|---|---|---|---|---|---|---|---|
C | Mn | Si | P | S | Cr | Mo | Ni | |
GE B50A947 A1, A2, A3, A5 | 0.09-0.15 | 0.25-0.80 | Max 0.5 | Max 0.03 | Max 0.030 | 12.25-13.0 | Max 0.3 | Max 0.60 |
GE B50A947 A4 | 0.09-0.15 | 0.25-0.80 | Max 0.5 | Max 0.025 | Max 0.010 | 12.25-13.0 | Max 0.3 | Max 0.60 |
GE B50A947 B1, B2, B3 | 0.12-0.15 | 0.25-0.65 | Max 0.5 | Max 0.025 | Max 0.010 | 11.50-12.50 | Max 0.3 | Max 0.75 |
SIEMENS 10705BC | 0.08-0.15 | Max 1.5 | Max 1.0 | Max 0.04 | Max 0.030 | 11.5-13.5 | Max 0.75 | |
X12CrS13, 1.4005 | 0.06-0.15 | Max 1.5 | Max 1.0 | Max 0.04 | 0.15-0.35 | 12.0-14.0 | Max 0.6 | |
X15Cr13, 1.4024 | 0.12-0.17 | Max 1.0 | Max 1.0 | Max 0.04 | Max 0.030 | 12.0-14.0 | ||
BS 410S21, 410S21 | 0.09-0.15 | Max 1.0 | Max 1.0 | Max 0.04 | Max 0.030 | 11.5-13.5 | Max 1.00 | |
UNS S41000, AISI 410, Grade 410 | Max 0.15 | Max 1.0 | Max 1.0 | Max 0.04 | Max 0.030 | 11.5-13.5 |
Mechanical Properties
403 Mechanical properties acc. to GE B50A947
- A1, A2
- After extrusion to compressor blades the requirements shall meet the requirements of P3C-AG60
- A 1, Brinell Hardness, 3000Kg Load: 241 Max
- A 2, Brinell Hardness, 3000Kg Load: 241 - 302
- A3, A4
- Tensile strength ksi(MPa) %, min: 110(760)
- Yield Strength 0.02% Offset ksi(MPa) min: 80(555)
- Elong In 2 inches %, min: 18
- RA %, min: 50
- Brinell Hardness, 3000Kg load: 223-269
- V-Notch Charpy min. Energy at R.T. ft-lbs(J) 40(54.2)
- A5
- Tensile strength ksi(MPa) %, min: 100
- Yield Strength 0.02% Offset ksi(MPa) min: 70
- Elong In 2 inches %, min: 15
- RA %, min: 40
- Brinell Hardness, 3000Kg load: 207-241
- V-Notch Charpy min. Energy at R.T. ft-lbs(J) -
- B1, B2
- Tensile strength ksi(MPa) %, min: 110(760)(
- Yield Strength 0.02% Offset ksi(MPa) min: 80(555)
- Elong In 2 inches %, min: 18
- RA %, min: 55
- Brinell Hardness, 3000Kg load: 223-269
- V-Notch Charpy min. Energy at R.T. ft-lbs(J) 25(33.9)
- B3
- Tensile strength ksi(MPa) %, min: 120(830)
- Yield Strength 0.02% Offset ksi(MPa) min: 90(620)
- Elong In 2 inches %, min: 18
- RA %, min: 55
- Brinell Hardness, 3000Kg load: 248-285
- V-Notch Charpy min. Energy at R.T. ft-lbs(J) 25(33.9)
403 Mechanical properties acc. to EN 10088-1
- Tensile strength Rm = 650 - 850 MPa
- Yield point Re: >450 MPa
- Elongation A > 15%
- Modulus of elasticity E = 215 GPa
- Thermal conductivity coefficient λ = 30 W ⋅ m-1 ⋅ K-1
- Thermal capacity cp = 460 J ⋅ kg-1 ⋅ K-1
- Hardness in softened state 121 - 187 HB
Physical Properties
Elastic Modulus (GPa) | Mean Coefficient of Thermal Expansion (μm/m/°C) | Thermal Conductivity (W/m.K) | Specific Heat 0-100 °C (J/kg.K) | Electrical Resistivity (nΩ.m) | |||||
---|---|---|---|---|---|---|---|---|---|
0-100 °C | 0-315 °C | 0-538 °C | at 100 °C | at 500 °C | |||||
410 | 7800 | 200 | 9.9 | 11 | 11.5 | 24.9 | 28.7 | 460 | 570 |
Heat Treatment
403 steels have good scaling resistance at temperatures of up to 650 °C. However, the mechanical properties of the material will tend to reduce at temperatures ranging from 400 to 580 °C.
403 steels can be fully annealed at temperatures from 815 to 900 °C, followed by slow furnace cooling and air-cooling. Process annealing of grade 410 steels can be carried out at temperatures ranging from 650 to 760 °C and air-cooled. Hardening – Hardening of grade 410 steels can be performed at 925 to 1010 °C, followed by air and oil quenching. Heavy sections of grade 410 need to be oil quenched. Tempering, to enhance the mechanical properties and hardness of grade 410 steels, follows this process. It is not recommended to perform tempering at temperatures from 400 to 580 °C.
Welding Properties
403 steels can be welded using all conventional welding techniques, but the materials should pre-heated at 150 to 260 °C followed by post-weld annealing treatment, to mitigate cracking. 403 welding rods are recommended for tempering and post-hardening. In the "as welded" conditions, grade 309 filler rods can be used to achieve a ductile joint. According to AS 1554.6 standards, grade 309 electrodes or rods are preferred for welding 403 steels.
Machining Properties
403 steels can be easily machined in highly tempered or annealed conditions. However, it is hard to machine grade 410 steels if they are hardened above 30HRC. Free machining grade 416 is the best titleernative.
What is AISI 403 equivalent to?
AISI 403, AISI 410, UNS S40300, UNS S41000, 1.4006, 1.4011, X12Cr13, X12Cr12, SUS410