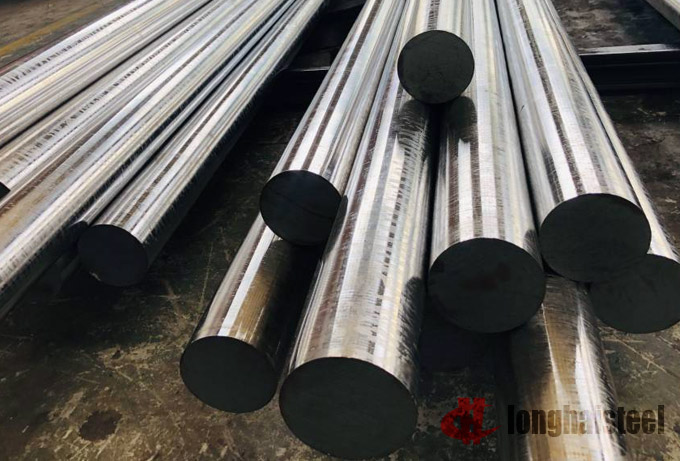
Alloy 825(UNS N08825) is an Austenitic Ni-Fe-Cr alloy with add of Mo, Cu and Ti. It was developed to provide exceptional resistance to numerous corrosive environments, both oxidizing and reducing. acc. to ASTM B 425, ASTM B 564. ASME SB 425, ASME SB 564, ASME SB 424. DIN 17744, 17752, 17750, 17753, 17754. ISO 6208, 9723, 9724, 9725. BS 3076NA16. API 5LD, 5LC.
- Heat Treatment
- Thermal Properties
- Welding
- Machining
- Similar or equivalents steel grade
What is Alloy 825(UNS N08825) grade steel?
Alloy 825(UNS N08825) is an Austenitic Ni-Fe-Cr alloy with add of Mo, Cu and Ti. It was developed to provide exceptional resistance to numerous corrosive environments, both oxidizing and reducing. high resistance to chloride-induced stress corrosion, chloride-induced pitting and crevice corrosion, oxidizing and non-oxidizing hot acids, toughness, even under continuous operation, at both room and elevated temperatures, up to approximately 550°C.
Alloy 825 Related Specifications
ASTM B 425, ASTM B 564. ASME SB 425, ASME SB 564, ASME SB 424. DIN 17744, 17752, 17750, 17753, 17754. ISO 6208, 9723, 9724, 9725. BS 3076NA16. API 5LD, 5LC.
Chemical Composition
Grade | Chemical composition WT % | |||||||||||||
---|---|---|---|---|---|---|---|---|---|---|---|---|---|---|
C | Si | Mn | P | S | Cr | Ni | Mo | Cu | Co | Ti | B | Al | Fe | |
2.4858, NiCr21Mo | Max 0.05 | Max 0.50 | Max 1.00 | Max 0.03 | Max 0.015 | 19.5-23.5 | 38-46 | 2.5-3.5 | - | - | 0.6-1.2 | - | Max 0.2 | 20-38 |
ISO NiFe30Cr21Mo3 | Max 0.05 | Max 0.50 | Max 1.00 | Max 0.03 | Max 0.015 | 19.5-23.5 | 38-46 | 2.5-3.5 | 1.5-3.0 | Max 1.50 | 0.6-1.2 | Max 0.2 | Bal | |
UNS N08825 | ||||||||||||||
AFNOR NC21FeDU | ||||||||||||||
JIS G7214 NiFe30Cr21Mo3 | Max 0.05 | Max 0.50 | Max 1.00 | - | Max 0.015 | 19.5-23.5 | 38-46 | 2.5-3.5 | 1.5-3.0 | - | 0.6-1.2 | Max 0.2 | Bal |
Mechanical Properties
Alloy 825 Mechanical properties acc. to ISO 9720
- Tensile strength Rm MPa: Min 590
- Yield Strength Rp MPa: Min 240
- A %: 30
Alloy 825 Mechanical properties acc. to JIS G7214
- +CW A
- Tensile strength Rm MPa: Min 590
- Yield Strength Rp MPa: Min 240
- A %: Min 30
- +HW A
- Tensile strength Rm MPa: Min 520
- Yield Strength Rp MPa: Min 170
- A %: Min 30
- Plate, Sheet, Strip, Coils All thickness or diameters
- Cold rolled deep drawing quality t ≥ 0.25 mm thk. HV about 210
- Cold rolled deep drawing quality t ≥ 0.25 mm thk. HR about 94
- Cold rolled deep drawing quality t ≥ 3 mm thk. HV about 210
- Cold rolled deep drawing quality t ≥ 3 mm thk. HR about 94
- Tensile strength Rm MPa: Min 590
- Yield Strength Rp MPa: Min 240
- A %: Min 30
- Hardness
Alloy 825 Mechanical properties acc. ISO 6208
Physical Properties
- Density: 8.14 g/cm3
- Melting: 1370-1400°C(2500-2550°F)
- Magnetic: Max 1.005
Heat Treatment
Soft or stabilizing annealing should be carried out at temperatures between 920°C and 980°C (1690 to 1800°F), preferably at 940 ±10°C (1725 ±15°F). Water quenching should be carried out rapidly to achieve optimum corrosion characteristics. Workpieces of less than 3 mm (0.12 in) thickness can be cooled down using air nozzles.
Heating
Workpieces must be clean and free of any contaminants before and during heat treatment. Sulfur, phosphorus, lead and other low-melting-point metals can lead to damages when heat treating Alloy 825. Sources of such contaminants include marking and temperature-indicating paints and crayons, lubricating grease and fluids, and fuels. Fuels should contain as little sulfur as possible. Natural gas should contain less than 0.1 wt.-% of sulfur. Heating oil with a sulfur content of maximum 0.5 wt.-% is also suitable. Electric furnaces are to be preferred due to precise temperature control and freedom from contamination due to fuel. The furnace atmosphere should be set between neutral and slightly oxidising, and should not change between oxidising and reducing. Direct flame impingement needs to be avoided.
Hot working
Alloy 825 may be hot-worked in the temperature range 1150°C to 900°C (2100°F to 1650°F) with subsequent rapid cooling down in water or by using air. The workpieces should be placed in the furnace heated to hot working temperature in order to heat up. Once the temperature has equalised, a retention time of 60 minutes for each 100 mm (4in) of workpiece thickness is recommended. After this, the workpieces should be removed immediately and formed during the stated temperature window. If the material temperature falls below the minimum hot working temperature, the workpiece must be reheated. Heat treatment after hot working is recommended in order to achieve optimum properties and corrosion resistance.
Cold working
Cold working should be carried out on annealed material. Alloy 825 has a higher work hardening rate than austenitic stainless steels. This must be taken into account during design and selection of forming tools and equipment and during the planning of the forming processes. Intermediate annealing may be necessary at high degrees of cold working deformation. After cold working with more than 15% of deformation the material should be soft annealed.
Thermal Properties
Temperature °C | Yield strength Rp 0.2 MPa | Tensile strength Rm MPa | Elongation A % |
---|---|---|---|
20 | 240 | 585 | 30 |
100 | 205 | 530 | |
150 | 190 | 525 | |
200 | 180 | 515 | |
250 | 175 | 510 | |
300 | 170 | 500 | |
350 | 165 | 495 | |
400 | 160 | 490 | |
450 | 155 | 485 |
Welding Properties
When welding nickel-base alloys and special stainless steels, the following instructions should be adhered to:
Workplace
A separately-located workplace, which is specifically separated from areas in which carbon steels are being processed, should be used. Maximum cleanliness is required, and draughts should be avoided during inert gas welding.
Auxiliary equipment and clothing Clean fine leather gloves and clean working clothes should be used.
Tools and machines
Tools used for other materials must not be used for nickel-base alloys and stainless steels. Brushes should be made of stainless materials. Processing and machining equipment such as shears, punches or rollers must be fitted with means (felt, cardboard, films) in order to avoid material contamination with ferrous particles, which can be pressed into the surface of the material and thus lead to corrosion.
Welding edge preparation
Welding edge preparation should preferably be carried out using mechanical methods such as lathing, milling or planing. Abrasive waterjet cutting or plasma cutting is also suitable. In the latter case, however, the cut edge (seam flank) must be cleanly re-worked. Careful grinding without overheating is acceptable.
Ignition
The arc may only be struck in the weld area, e.g. along the seam flanks or outlets, and should not be carried out on the workpiece surface. Arc striking areas are prone to corrosion.
Welding process
Alloy 825 can be joined to itself and to many other metals by conventional welding processes. These include GTAW (TIG), plasma arc, GMAW (MIG/MAG) and SMAW (MMA). Pulsed arc welding is the preferred technique. For the MAG process the use of a multi-component shielding gas (Ar + He + H2 + CO2) is recommended. For welding, Alloy 825 should be in the annealed temper and be free from scale, grease and markings. When welding roots, sufficient protection of the root needs to be ensured with pure argon (Ar 4.6) so that the welding seam is free of oxides after welding. Root backing is also recommended for the first intermediate pass following the initial root pass and in some cases even for the second pass, depending on the weld set-up. Any discoloration/heat tint should be removed preferably by brushing with a stainless steel wire brush while the weld metal is still hot.