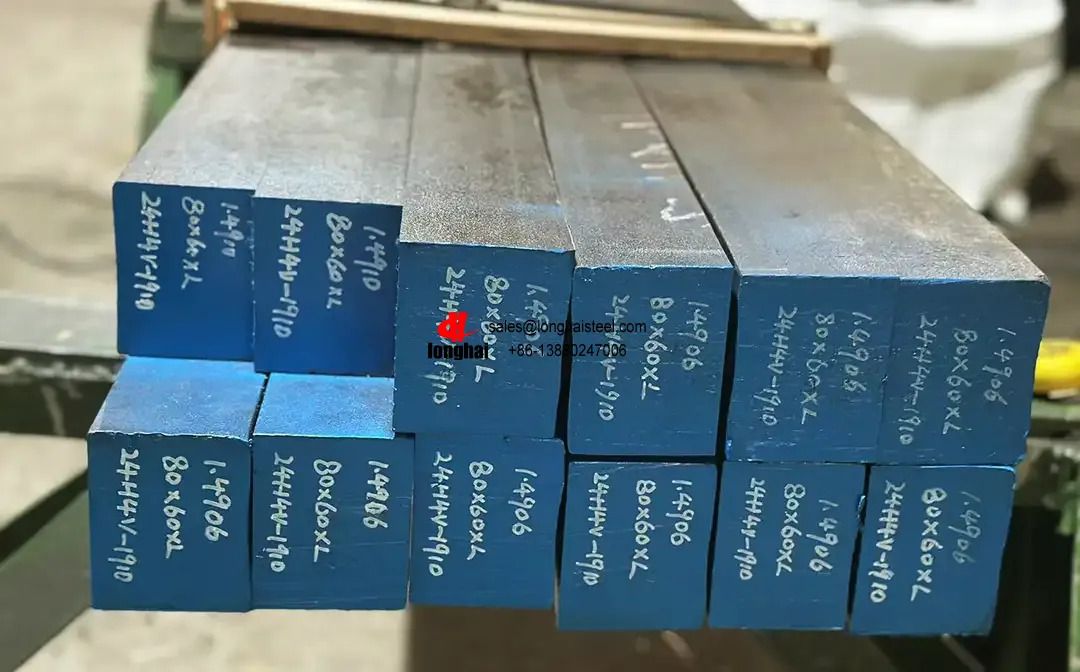
1.4906, X12CrMoWVNbN10-1-1 is a martensitic steel, which means it has a crystalline structure formed during heat treatment by rapidly cooling (quenching) from a high temperature. Martensitic steels are known for their high strength and hardness, making them suitable for demanding applications such as turbine blades, high-pressure valves, and other high-temperature components acc to SEW 555:2001-01 and Siemens MAT238053
What is 1.4906, X12CrMoWVNbN10-1-1 grade steel?
1.4906, X12CrMoWVNbN10-1-1 Alloy special steel for Gas Turbines, power plants, high-temperature applications, particularly in the construction of boilers, pressure vessels, and components for power plants, larger forgings, environments where high thermal stability and resistance to thermal fatigue are required, making it suitable for parts subjected to high pressures and temperatures acc to SEW 555:2001-01 and Siemens MAT238053 and TLV925812 This TLV is valid for steel bars with a 0.2% proof strength of 750 N/mm' minimum. Referenced Documents EN 10083-1, EN 10308, EN 10204, DIN EN ISO 6892-1, DIN EN ISO 148-1
Here's a breakdown of the designation:
X: Indicates that it is an alloy steel.
12: Refers to the approximate percentage of chromium in the alloy (12%).
Cr: Chromium, which is added to improve oxidation resistance and high-temperature strength.
Mo: Molybdenum, which enhances the strength and hardness of the steel at high temperatures.
W: Tungsten, which also contributes to high-temperature strength and wear resistance.
V: Vanadium, which improves strength and toughness.
Nb: Niobium, which contributes to the alloy's high-temperature stability and strength.
N: Nitrogen, which can improve strength and corrosion resistance.
10: Indicates the maximum carbon content (0.10%).
1-1: Additional information about the specific properties or manufacturing process of the steel.
Products Form:
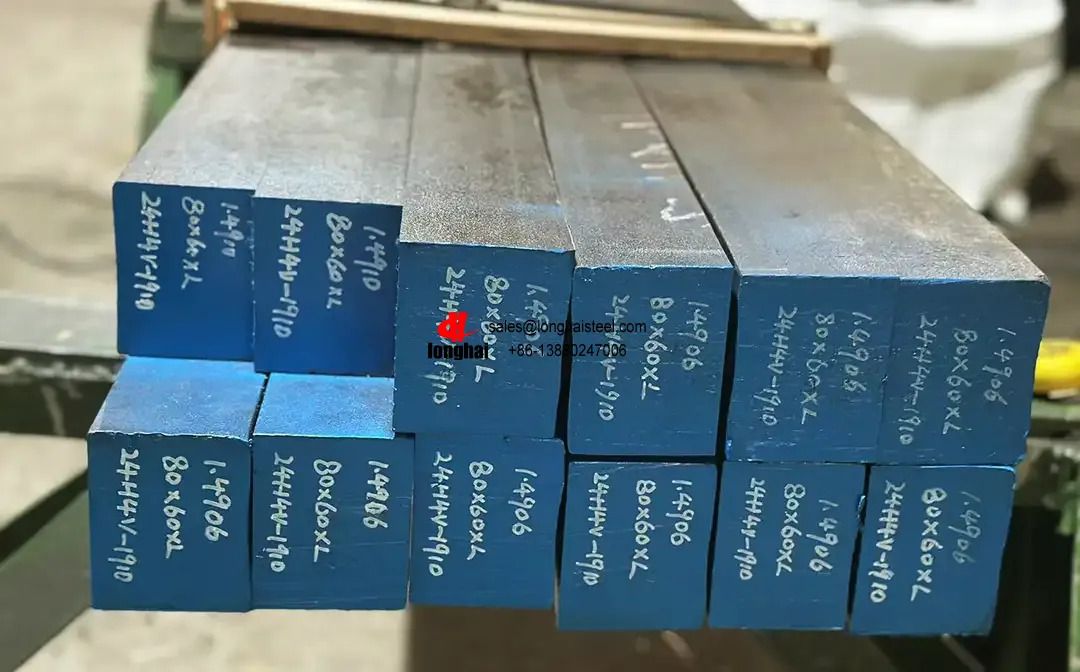
Chemical Composition
Grade | Chemical composition WT % | |||||||||||||
---|---|---|---|---|---|---|---|---|---|---|---|---|---|---|
C | Si | Mn | P | S | Cr | Ni | Mo | W | V | Nb | N | Al | As | |
1.4906, X12CrMoWVNbN10-1-1 acc. to MAT238053 | 0.10-0.14 | max. 0.10 | 0.40-0.60 | max. 0.015 | max. 0.007 | 10.00-11.00 | 0.60-0.80 | 1.00-1.20 | 0.95-1.10 | 0.15-0.25 | 0.04-0.06 | 0.04-0.06 | max. 0.012 | max. 0.012 |
B | Cu | Sb | Sn | Ti | ||||||||||
10 ppm | max. 0.01 | |||||||||||||
1.4906, X12CrMoWVNbN10-1-1 acc. to TLV 9258 12 | 0.11-0.13 | max. 0.12 | 0.40-0.50 | max. 0.010 | max. 0.005 | 10.2-10.8 | 0.7-0.8 | 1.0-1.1 | 0.95-1.05 | 0.15-0.25 | 0.04-0.06 | 0.045-0.06 | max. 0.01 | - |
Mechanical Properties
1.4906 Mechanical properties acc. to MAT238053 - Thickness* max. 1500mm
- Tensile strength Rm MPa: Min 800-950
- Proof strength Rp0.2 MPa: Min 700(A 50 MPa lower value applies for the core zones.)
- Elongation after fracture A %: T/Q min. 15/13((L0 = 5.65√S0)
- Red of area A%: T/Q min. 45/40
- KV J (+20ºC): T/Q min. 30/25
- Hardness HB: ca 280
1.4906 Mechanical properties acc. to TLV 9258 12 - Dia.* max. 100mm
- Tensile strength Rm MPa: max 1000
- Proof strength Rp0.2 MPa: 750-830
- Elongation after fracture A %: L min. 14 / T -LHSS
- Red of area A%: L min. 50 / T -LHSS
- KV J (+20ºC): L min. 40 / T -LHSS(Minimum value from 3 Charpy V-notch specimens wechat:specialsteel)
- Hardness HB30: 265-310
1.4906 Mechanical properties acc. to TLV 9258 12 - Dia.* min. 100mm
- Tensile strength Rm MPa: max 1000
- Proof strength Rp0.2 MPa: 750-830
- Elongation after fracture A %: T min. 13 / L -LHSS
- Red of area A%: T min. 40 / L -LHSS
- KV J (+20ºC): T min. 24 / L -LHSS(Minimum value from 3 Charpy V-notch specimens wechat:specialsteel)
- Hardness HB30: 265-310
Physical Properties
Physical Properties of X12CrMoWVNbN10-1-1 Steel
X12CrMoWVNbN10-1-1 is a martensitic steel known for its excellent high-temperature strength, creep resistance, and durability. Below are the typical physical properties of this steel:
- Density: Approximately 7.8 g/cm³.
- Melting Point: Around 1,420–1,450°C (2,588–2,642°F).
- Thermal Conductivity:
- At room temperature: ~24 W/m·K.
- Decreases slightly at elevated temperatures.
- Coefficient of Thermal Expansion:
- ~10.5 x 10⁻⁶ /K (in the range of 20–500°C).
- Elastic Modulus:
- Approximately 210 GPa at room temperature.
- Specific Heat Capacity:
- ~460 J/kg·K at room temperature.
Heat Treatment
1.4906, X12CrMoWVNbN10-1-1 Hardening acc. to MAT238053
- 1050ºC ±10ºC for at least 12 h. Cooling in oil.
- Tempering I: 570ºC ±10ºC, furnace cooling to 400ºC, thereafter cooling in air.
- Tempering II: 690ºC ±10ºC, furnace cooling to 400ºC, thereafter cooling in air.
1.4906, X12CrMoWVNbN10-1-1 Hardening acc. to TLV 9258 12 - wechat:specialsteel
The hardening temperature has to be between 1050ºC and 1100°C (air or liquid quenching) After hardening the forging must be cooled down to atemperature max. 100ºC in the center to guaranteecomplete transformation into martensite throughoutin the whole section.
A two-step tempering treatment must be performedconsidering the following: The first tempering stepmust be carried outbetween 570°and 680°C.The temperature for the second tempering stepmust be between 680 and 720°C If bars need to be straightened after the heat treat.ment, a stress relieving treatment shall be performedafter completion of the entire straightening process.Stress relieving is to be carried out at 20-50K below the tempering temperature with a subsequentslow cooling rate.wechat:specialsteel
Thermal Properties
Thermal Properties of X12CrMoWVNbN10-1-1 Steel
X12CrMoWVNbN10-1-1 is a martensitic steel specifically engineered for high-temperature applications. Its thermal properties are crucial for its performance in environments like gas turbines and power plants. Below are its key thermal characteristics:
-
Thermal Conductivity:
- At room temperature (~20°C): ~24 W/m·K.
- At elevated temperatures, thermal conductivity decreases slightly. For example, at 500°C, it typically ranges around 21–22 W/m·K.
-
Specific Heat Capacity (Cp):
- At room temperature (~20°C): ~460 J/kg·K.
- Increases moderately with temperature; at ~500°C, it ranges from 550 to 600 J/kg·K.
-
Coefficient of Thermal Expansion (CTE):
- From 20°C to 500°C: ~10.5 x 10⁻⁶ /K.
- From 20°C to 700°C: ~11.5 x 10⁻⁶ /K.
-
Thermal Stability:
- This steel maintains structural integrity at elevated temperatures, typically up to 600–650°C, making it suitable for turbine blades, high-temperature fasteners, and similar applications.
-
Heat Resistance:
- Exceptional resistance to thermal creep, oxidation, and fatigue, critical for prolonged exposure to high temperatures under stress.
Welding Properties
Welding Characteristics of X12CrMoWVNbN10-1-1 Steel
Welding X12CrMoWVNbN10-1-1, a high-strength martensitic steel, requires careful attention to avoid issues like cracking, distortion, and loss of mechanical properties. Below are the key considerations for welding this material:
1. Welding Methods
- Preferred Methods:
- Gas Tungsten Arc Welding (GTAW/TIG)
- Gas Metal Arc Welding (GMAW/MIG)
- Shielded Metal Arc Welding (SMAW) with suitable electrodes
- Other Possible Methods: Submerged Arc Welding (SAW), provided heat input is carefully controlled.
2. Preheating
- Importance: Preheating reduces thermal gradients and the risk of cold cracking.
- Typical Preheat Temperature: 200–300°C (392–572°F) before welding.
3. Interpass Temperature
- Maintain between 200–350°C (392–662°F) during welding to ensure uniformity and avoid residual stresses.
4. Post-Weld Heat Treatment (PWHT)
- Necessity: PWHT is critical to restore mechanical properties, relieve residual stresses, and minimize the risk of hydrogen-induced cracking.
- Typical PWHT Procedure:
- Heating to ~730–780°C (1,346–1,436°F)
- Holding for 1–2 hours depending on the thickness
- Controlled cooling to room temperature.
5. Filler Material
- Use matching or compatible filler materials to maintain alloy composition and mechanical properties. For X12CrMoWVNbN10-1-1, fillers with similar Cr, Mo, W, and Nb contents are recommended.
6. Shielding Gas
- Use inert or slightly reducing shielding gases (e.g., Argon or Argon-Helium mixtures) to protect the weld pool from oxidation.
7. Common Challenges
- Cracking: Preheat and PWHT mitigate cold cracking and stress-induced cracking.
- Distortion: Controlled heat input and clamping techniques help minimize distortion.
- Porosity: Ensure proper cleaning and use of low-hydrogen welding consumables.
Applications of Welded X12CrMoWVNbN10-1-1
- Components for gas turbines, boilers, and heat exchangers, where both high strength and temperature resistance are essential.
Machining Properties
Machining Characteristics of X12CrMoWVNbN10-1-1 Steel
X12CrMoWVNbN10-1-1 is a high-strength, heat-resistant martensitic steel designed for demanding applications. Its machinability is moderately challenging due to its high hardness and tendency to work harden. Proper techniques and tooling are essential for efficient machining.
1. General Machinability
- Machinability Rating: Low to moderate, depending on the material's heat treatment condition.
- Annealed Condition: Easier to machine due to reduced hardness.
- Hardened Condition: More challenging due to increased strength and wear resistance.
2. Recommended Cutting Tools
- Tool Material:
- Carbide-tipped tools for general machining.
- CBN (Cubic Boron Nitride) or ceramic tools for high-precision or hardened material machining.
- Coatings: TiN (Titanium Nitride) or TiAlN (Titanium Aluminum Nitride) coatings enhance tool life by reducing heat and wear.
3. Cutting Parameters
- Cutting Speed: Lower speeds to minimize heat and tool wear: ~20–40 m/min for carbide tools in hardened material.
- Feed Rate: Moderate feed rates to balance tool wear and surface finish: ~0.1–0.3 mm/rev.
- Depth of Cut: Avoid excessive depth to prevent tool damage; start with 0.5–2.0 mm depending on the operation.
4. Coolant and Lubrication
- Use water-soluble cutting fluids or oils to reduce heat and improve surface quality.
- Flood cooling is preferred for continuous operations to manage thermal effects.
5. Machining Techniques
- Turning: Use rigid setups and adjust speeds to prevent vibrations.
- Milling: Opt for smaller depths of cut with high-speed milling for precision.
- Drilling: Employ cobalt-alloyed drills or carbide drills; use peck drilling for deep holes to avoid chip clogging.
- Grinding: Suitable for final finishing; use aluminum oxide or silicon carbide grinding wheels.
6. Challenges in Machining
- Tool Wear: High resistance to cutting causes accelerated wear; frequent tool changes may be required.
- Heat Generation: Proper cooling and low speeds reduce excessive heat buildup.
- Work Hardening: Avoid prolonged cutting in one spot; maintain continuous motion.
Applications of Machined X12CrMoWVNbN10-1-1
- High-temperature turbine blades, fasteners, and components requiring tight tolerances and high precision.
What is 1.4906, X12CrMoWVNbN10-1-1 equivalent to?
Similar Grades to X12CrMoWVNbN10-1-1 Steel
X12CrMoWVNbN10-1-1 is a high-strength martensitic steel with excellent heat resistance and creep strength, typically used in high-temperature applications like gas turbines and power plants. Below are some grades that are considered similar in composition, properties, or applications:
1. European Standards (EN)
- X12CrMoWVNb12-1 (1.4923): A closely related martensitic steel with similar high-temperature properties, used in turbines and boilers.
- X12CrMoVNbN9-1 (P91): Often used in high-pressure and high-temperature environments, with slightly lower tungsten content.
2. American Standards (ASTM/ASME)
- Grade 91 (P91/T91): A ferritic-martensitic steel with comparable creep strength, used in power generation and petrochemical industries.
- Grade 92 (P92/T92): Contains higher levels of tungsten and niobium, offering enhanced creep resistance and similar performance.
3. Japanese Standards (JIS)
- STBA29: Martensitic steel used in heat-resistant applications, similar to X12CrMoWVNbN10-1-1.
- STBA28: Another comparable grade, often used in boiler and turbine construction.
4. Other Comparable Grades
- 10CrMoW9-10: Used in similar applications but with lower niobium and vanadium content.
- X20CrMoV12-1: A martensitic stainless steel with similar thermal and mechanical properties.
- AISI 422 (UNS S42200): A martensitic stainless steel with comparable high-temperature strength, often used in aerospace and turbine applications.
Key Differences to Note
- W and Nb Content: X12CrMoWVNbN10-1-1 contains higher tungsten and niobium, enhancing its strength at elevated temperatures.
- Application-Specific: Selection depends on exact operating conditions like temperature, pressure, and environmental factors.