AISI 422 Stainless Steel experiment and method
January 09,2023
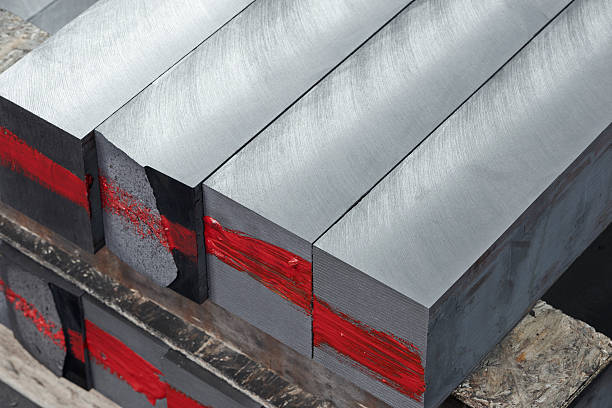
The steel used in the experiment is 422 martensitic stainless steel, its chemical composition is shown in Table 2.1, and the original heat treatment state is hot-rolled and annealed. In order to ensure the consistency and uniformity of the composition and performance of the steel used in the experiment, the sample adopts a Φ8mm 12mm cylinder cut along the rolling direction on the rolled bar and polished smooth to reduce the influence of friction on the experimental results.
In order to study the plastic forming properties and microstructure changes, unidirectional isothermal thermal simulation compression experiments were carried out on 422 martensitic stainless steel on the Gleeble-3500 thermal simulation testing machine. The Gleeble-3500 thermal simulation testing machine is controlled by computer programming, which can accurately control the heating temperature, strain rate, strain and other forming process parameters during the deformation process, and realize real-time tracking of experimental data and electronic transient recording. It can collect a large number of data, and the data stability and repeatability are high. The entire thermal simulation compression experiment process is carried out under the protection environment of argon gas, which can effectively avoid the oxidation of 422 martensitic stainless steel at high temperature. A thermocouple is welded in the middle of the sample to monitor the temperature change during thermal compression. Put tantalum sheets at both ends of the sample and coat with lubricant to reduce the friction effect between the indenter and the sample, reduce heat loss, increase the uniformity of sample deformation, and reduce experimental errors.
When performing thermal simulation compression experiments on 422 martensitic stainless steel, the sample is first heated to 1250°C at a heating rate of 10°C/s, and kept for 3 minutes, so that the alloy is fully austenitized and a uniform austenite structure is obtained; Then the sample is slowly cooled to the deformation temperature at a cooling rate of 5°C/s, and held for 10s to eliminate the temperature gradient difference inside the sample, reduce the deformation error, and improve the measurement accuracy of the material's high-temperature flow stress. Finally, perform unidirectional thermal compression at a predetermined strain rate to compress the sample to a specified deformation, measure the true stress-true strain curve of the alloy, and immediately perform water cooling and quenching on the compressed sample to retain the thermal deformation at high temperature organize. The process flow of the thermal simulation compression experiment of 422 martensitic stainless steel is shown in 2.1. The deformation temperature range is 850~1100℃, the strain rate range is 0.005~5s-1, and the strain range is 0.2~0.7. According to the experimental design, a total of 48 thermal compression experiments are required, and the sample after thermal compression is shown in Figure 2.2.
Metallographic experiment is to observe and measure the structure, distribution and grain size of materials under an optical microscope. It is the most commonly used experimental method for low-magnification structure research and analysis of metal materials. In this experiment, the observation and analysis of the internal structure of 422 stainless steel after compression deformation is an extremely important step in the research of this paper. The sample compressed by thermal simulation is in the shape of a round cake, which is cut in half along the direction of the compression axis, and the cut surface of the sample is taken on sandpaper of different grain sizes, and ground in order from coarse to fine , after the surface is smooth, move it to the polishing machine to polish until the mirror surface. Finally, the polished and polished samples were corroded with the prepared etchant, cleaned and dried, and taken to a metallographic microscope for metallographic observation.