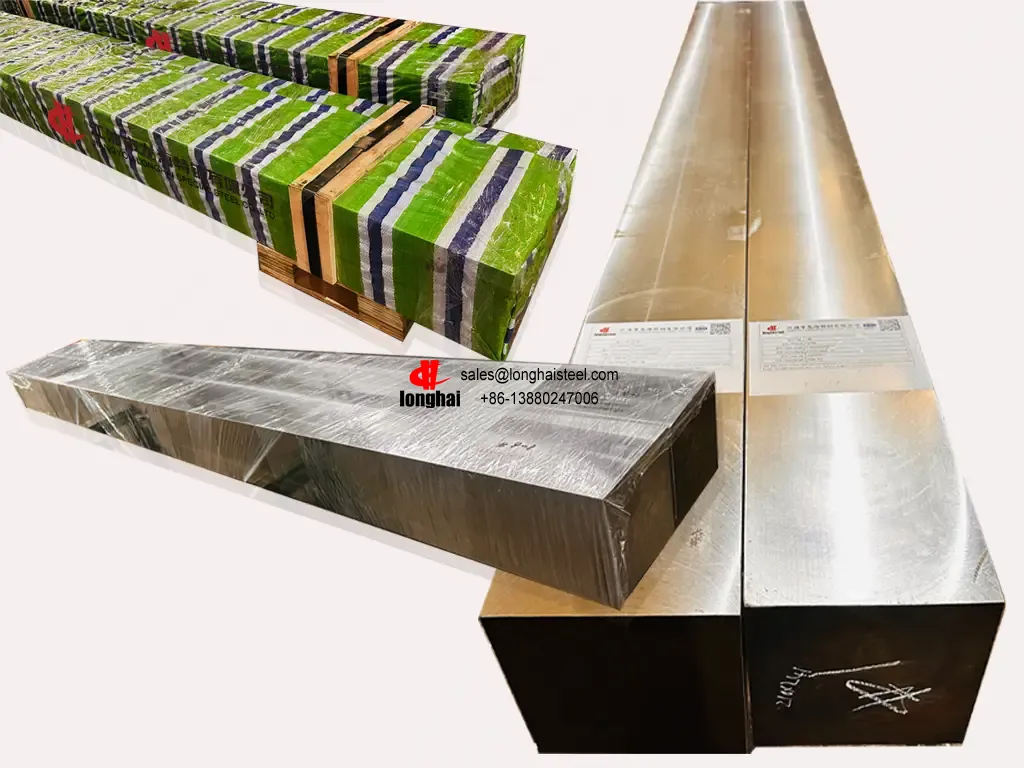
403Cb+ ESR Stainless, Alloy Steel for Fasteners. 403Cb+ steel is EN 10269 heat-resistant steel and is used for fasteners.
- Heat Treatment
- Thermal Properties
- Welding
- Machining
- Similar or equivalents steel grade
What is B50A365 B, 403Cb+ grade steel?
403Cb+ ESR Stainless, Alloy Steel for Fasteners. 1.4913 steel is EN 10269 heat-resistant steel and is used for fasteners. 403Cb+ martensitic stainless steel is characterized by high-temperature strength and creep resistance. titlehough the alloy content of chromium and molybdenum, which are elements for high temperatures, is small, vanadium, which is an element for tool steel, Nitrogen, which increases strength as an interstitial element, increases high-temperature strength and creep.
Niobium alloy is used for bolts and nuts for power plants, parts for aircraft, steam valves, Use temperature up to 580℃ for turbine blades and shafts, oil production equipment. EN material number 1.4913, material name X19CrMoMbV11-1, DIN 1.4914, Comparable to SUH600, Alloy Grade H46, 403Cb Plus, B50A365 materials.
It is a material used for QT heat treatment and has a minimum yield strength of 750 MPa during QT heat treatment.
In Soft Annealed condition, HBW 302 maximum.
By removing impurities and non-metallic inclusions inside the steel, the toughness and internal
Electro Slag Remelt (ESR) is sometimes used to improve quality.
Inclusions
Non metallic particles like oxides, sulfides, and silicates in the steel matrix. To decrease the negative effect of inclusions on mechanical properties,
special cleaning methods are used during the melting process in steel production.
It refers to very small particles such as oxides, sulfides, and silicates in the metal structure.
They are used in the manufacturing process of steel to reduce the negative effect on mechanical properties.
remove it.
Niobium (Nb) or Columbium (Cb)
When niobium is alloyed with steel, it contributes to the improvement of strength by refining the crystal grains.
It serves to improve high-temperature strength and creep performance.
Vanadium (V) – increases shock resistance, strength, and hardness.
Retards grain growth even after exposure to high temperatures.
Elemental vanadium increases hardness, strength and impact resistance, An element that retards grain growth at high temperatures.
In addition, it increases wear resistance and elasticity limit, refines the structure, and has a specific gravity of 6.16 g/cm
In the case of plate, the yield strength is 450 MPa, and when cold rolled (84%), it is 770MPa. Ni, Cr, Mo elements and they are often alloyed together.
Products Form:
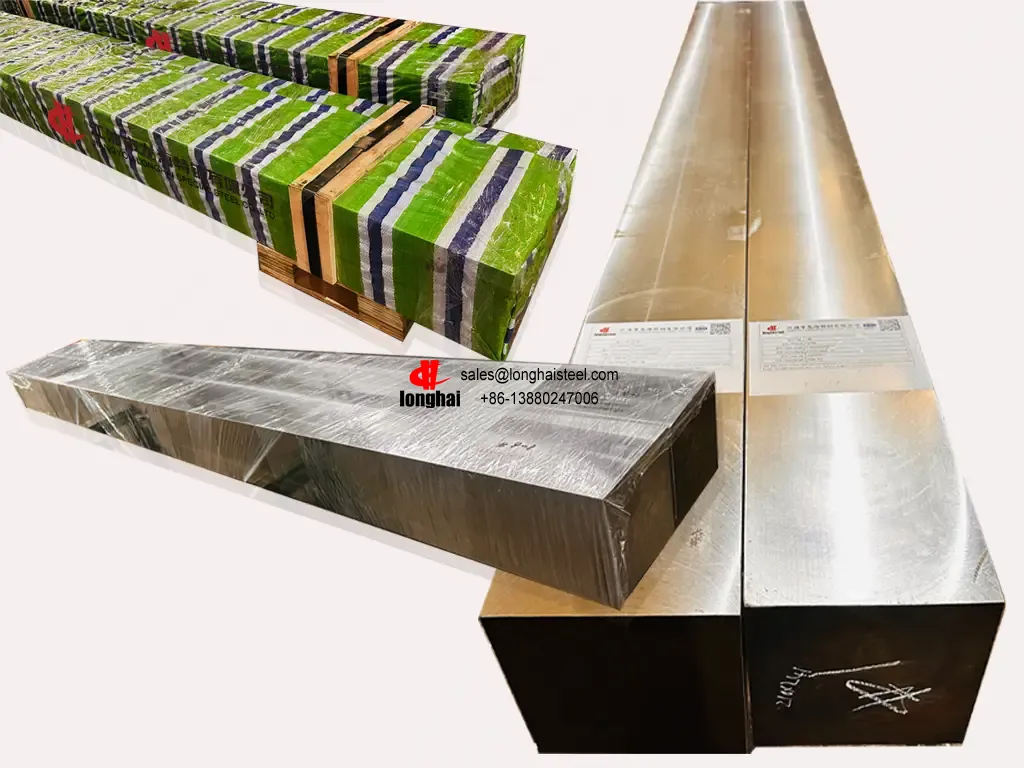
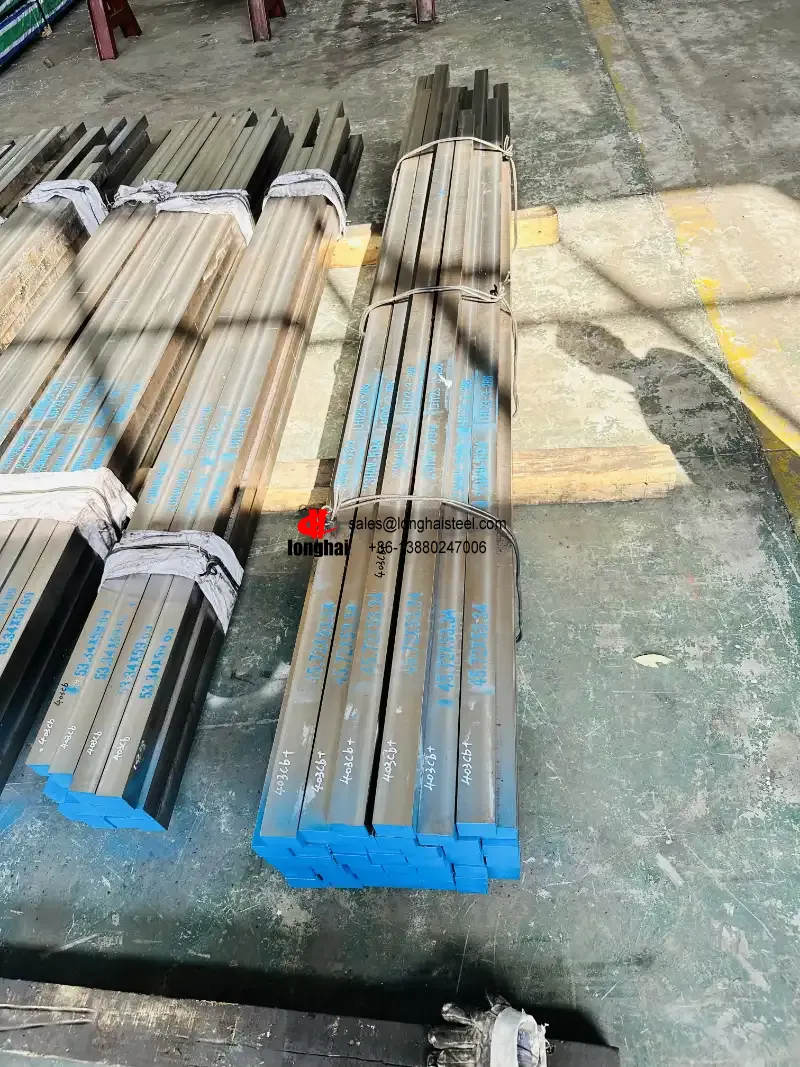
Chemical Composition
Grade | Chemical composition WT % | |||||||||||||||
---|---|---|---|---|---|---|---|---|---|---|---|---|---|---|---|---|
C | Si | Mn | P | S | Cr | Ni | Nb | V | N | Pb | Sn | Ti | Al | W | Co | |
403Cb+, B50A365 A | 0.15-0.20 | 0.20-0.60 | 0.50-0.80 | 0.025 | 0.025 | 10.0-11.0 | 0.30-0.60 | 0.35-0.55 | 0.15-0.25 | 0.04-0.08 | 0.005 | 0.04 | 0.05 | 0.05 | 0.25 | 0.25 |
403Cb+, B50A365 B | 0.15-0.20 | 0.20-0.60 | 0.50-0.80 | 0.020 | 0.010 | 10.0-11.0 | 0.30-0.60 | 0.35-0.55 | 0.15-0.25 | 0.04-0.08 | 0.005 | 0.04 | 0.05 | 0.05 | 0.25 | 0.25 |
403Cb+, B50A365 A1 | 0.15-0.20 | 0.20-0.60 | 0.50-0.80 | 0.025 | 0.025 | 10.0-11.0 | 0.30-0.60 | 0.35-0.55 | 0.15-0.25 | 0.04-0.08 | 0.005 | 0.04 | 0.05 | 0.05 | 0.25 | 0.25 |
Mechanical Properties
Mechanical properties acc. to B50A365 Class A, B, C
- Tensile Strength, ksi (MPa), min 140 (965)
- Yield Stress 0.02% Offset, ksi (MPa), min 100 (690)
- Elongation in 4D %, min 15
- Reduction of Area, %, min 45
- Hardness, Brinell 3000 Kg load 321 max.
- Impact, Charpy V-Notch, Ft.-Lbs. (J), min 8 (11)
Physical Properties
1. Density: The density of 403Cb+ stainless steel is typically around 7.75 grams per cubic centimeter (g/cm³).
2. Melting Point: The melting point of 403Cb+ stainless steel is around 1425-1450 degrees Celsius (2600-2642 degrees Fahrenheit).
3. Hardness: 403Cb+ stainless steel can achieve a high hardness level through heat treatment. It can range from about 30 to 40 on the Rockwell C scale (HRC).
4. Strength: This stainless steel has a high tensile strength, typically in the range of 900-1100 megapascals (MPa).
5. Corrosion Resistance: 403Cb+ stainless steel exhibits good resistance to corrosion in various environments, including mild acids and alkalis. However, it may not be as corrosion-resistant as some other stainless steel grades, such as 316 or 304.
It's important to note that the specific physical properties of 403Cb+ stainless steel can vary depending on the manufacturing process and any additional heat treatments it undergoes. Therefore, it is always recommended to refer to the manufacturer's specifications for precise details on the physical properties of this particular stainless steel grade.
Heat Treatment
(1095-1135°C) and held at temperature for sufficient time to assure uniform temperature within the load and each part thereof. The material shall then be quenched in oil or rapidly moving air, as approved in the manufacturing process plan,to a temperature below the Mf martensite finish temperature, to assure complete transformation. Material made to Classes A and C and material that is made to Class B without straightening or cold finishing shall then be uniformly heated to a minimum tempering temperature of 1185°F (640°C), and held for the time necessary to achieve all of the required properties.
Welding Properties
403Cb+ stainless steel can be welded using various methods, including TIG (Tungsten Inert Gas) welding, MIG (Metal Inert Gas) welding, and stick welding (SMAW - Shielded Metal Arc Welding). However, it is important to take certain precautions and follow proper welding practices to ensure successful welds and maintain the desired properties of the material.
Here are some considerations for welding 403Cb+ stainless steel:
1. Preheating: Preheating the material before welding can help reduce the risk of cracking. The recommended preheating temperature typically falls in the range of 200-400°C (392-752°F), depending on the thickness of the material.
2. Post-weld Heat Treatment: Performing a post-weld heat treatment (PWHT) can help alleviate stresses and improve the weld's mechanical properties. The specific temperature and duration of the PWHT will depend on the requirements of the application and the desired properties of the weld.
3. Filler Metal: It is important to select an appropriate filler metal for welding 403Cb+ stainless steel. Generally, austenitic stainless steel filler metals, such as ER308 or ER309, are commonly used. These filler metals provide good corrosion resistance and match the strength of the base material.
4. Welding Technique: Proper welding technique is crucial to ensure a high-quality weld. Techniques like maintaining a consistent travel speed, proper shielding gas flow, and maintaining a suitable arc length should be followed.
5. Post-weld Cleaning: After welding, it is recommended to clean the weld area thoroughly to remove any spatter or other contaminants. This can be done using appropriate cleaning agents and methods to ensure the integrity and appearance of the weld.
It is important to note that the specific welding parameters and procedures may vary depending on the specific application and requirements. Therefore, it is advisable to consult the manufacturer's recommendations or seek the guidance of a qualified welding professional for precise welding procedures for 403Cb+ stainless steel.
Machining Properties
403Cb+ stainless steel is a high-strength, heat-resistant, and corrosion-resistant material commonly used in various industries. Machining this material requires careful consideration of its properties and proper machining techniques to achieve desired results.
Here are some considerations for machining 403Cb+ stainless steel:
1. Tool Selection: Selecting the appropriate cutting tool is crucial for machining 403Cb+ stainless steel. It is recommended to use high-speed steel (HSS) or carbide tools specifically designed for stainless steel machining. These tools offer good heat resistance and cutting performance.
2. Cutting Speed: Maintaining the appropriate cutting speed is important to prevent excessive heat buildup and tool wear. It is advisable to use lower cutting speeds compared to carbon steels. The specific cutting speed will depend on the tool material, tool geometry, and machining conditions.
3. Feed Rate: The feed rate should be adjusted to ensure efficient material removal while avoiding excessive tool wear. A slower feed rate is generally recommended for machining stainless steels to minimize heat generation and extend tool life.
4. Coolant/Lubricant: Using a coolant or lubricant during machining is essential to dissipate heat and improve chip formation. Water-soluble cutting fluids or specific lubricants designed for stainless steels can be used to enhance machining performance.
5. Rigidity: Ensure that the workpiece, tool, and machine setup are rigid to minimize vibration and chatter during machining. Vibration can negatively affect surface finish and tool life.
6. Chip Control: Proper chip control is important to avoid chip clogging, which can lead to poor surface finish and tool damage. Using appropriate chip breakers, chip evacuation methods, or chip control inserts can help improve chip control.
7. Post-Machining: After machining, it is recommended to clean the machined surfaces to remove any cutting fluids, chips, or contaminants. This can be done using suitable cleaning agents and methods to ensure the desired surface finish and cleanliness.
It is important to note that the specific machining parameters and techniques may vary depending on the specific application and requirements. Therefore, it is advisable to consult the manufacturer's recommendations or seek the guidance of a qualified machining professional for precise machining procedures for 403Cb+ stainless steel.
B50A365, B50A365B, 403Cb+ Steels of Blade for Steam and Gas Turbine stock list
Steel Grade | Shape | Dimension(mm) | Quantity(PCs) | Weight(Kg) | Condition | Smelt |
---|
What is B50A365 B, 403Cb+ equivalent to?
403Cb+, 1.4913, 1.4913, X19CrMoMbV11-1, 1.4914, SUH600, Alloy Grade H46, 403Cb Plus, B50A365